Lean 3P Workshop: Successful Stakeholder Engagement in Facility Design
Why using the Production Preparation Process model is an effective tool for health care architects to gather, distill and incorporate all parties' considerations into a new construction or renovation of a facility, according to E4H Environments for Health Architecture's Regan Henry and Mike Bennett.
By Regan Henry & Mike Bennett, Health Care Architects, E4H Environments for Health Architecture
When approaching a renovation or new construction, hospital systems have a wide variety of interests to consider. As health care architects and designers, we work to ensure the needs of everyone who steps foot in a facility are met in an efficient, sustainable and health-promoting way. It is our responsibility—and a great opportunity—to work closely with administrative and medical personnel to understand their day-to-day workflow and design a responsive facility plan.
A Lean 3P workshop (named for the Production Preparation Process) is an effective tool for gathering, distilling and incorporating specific considerations into a new design. The workshop is based on four key concepts: eliminate waste, focus on process and function, make durable decisions and ensure collaborative participation. It harnesses the efforts of many stakeholders into a consolidated multi-day planning session that enables rapid creation and testing of design options. Instead of hosting isolated discussions and receiving feedback in the later stages of design, one central event cultivates the evolution of a design and promotes end-user buy-in.
Our recent session constructing a new schematic plan for the renovation of Lifespan Health System’s Newport Hospital Emergency Department offers a look into this process. Below are seven key takeaways.
Invite a wide array of stakeholders
It’s important to create an inclusive environment to foster informed decision-making. With extremely diverse job functions, a doctor will have different needs from a maintenance worker, who will have a different perspective from an HR coordinator. To ensure a new or renovated facility works effectively for everyone, it is critical to get all users’ input at an early stage. At Newport Hospital in Rhode Island, E4H Environments for Health Architecture hosted more than 70 individuals across departments: administrators, physicians, nurses, supply chain, IT, security, maintenance and utility workers, as well as past patients. Each offered their take on how to improve the physical space they all share. The result was a final design that addressed desired future state work flows and enabled the greatest efficiency of movement.
Diversify into teams
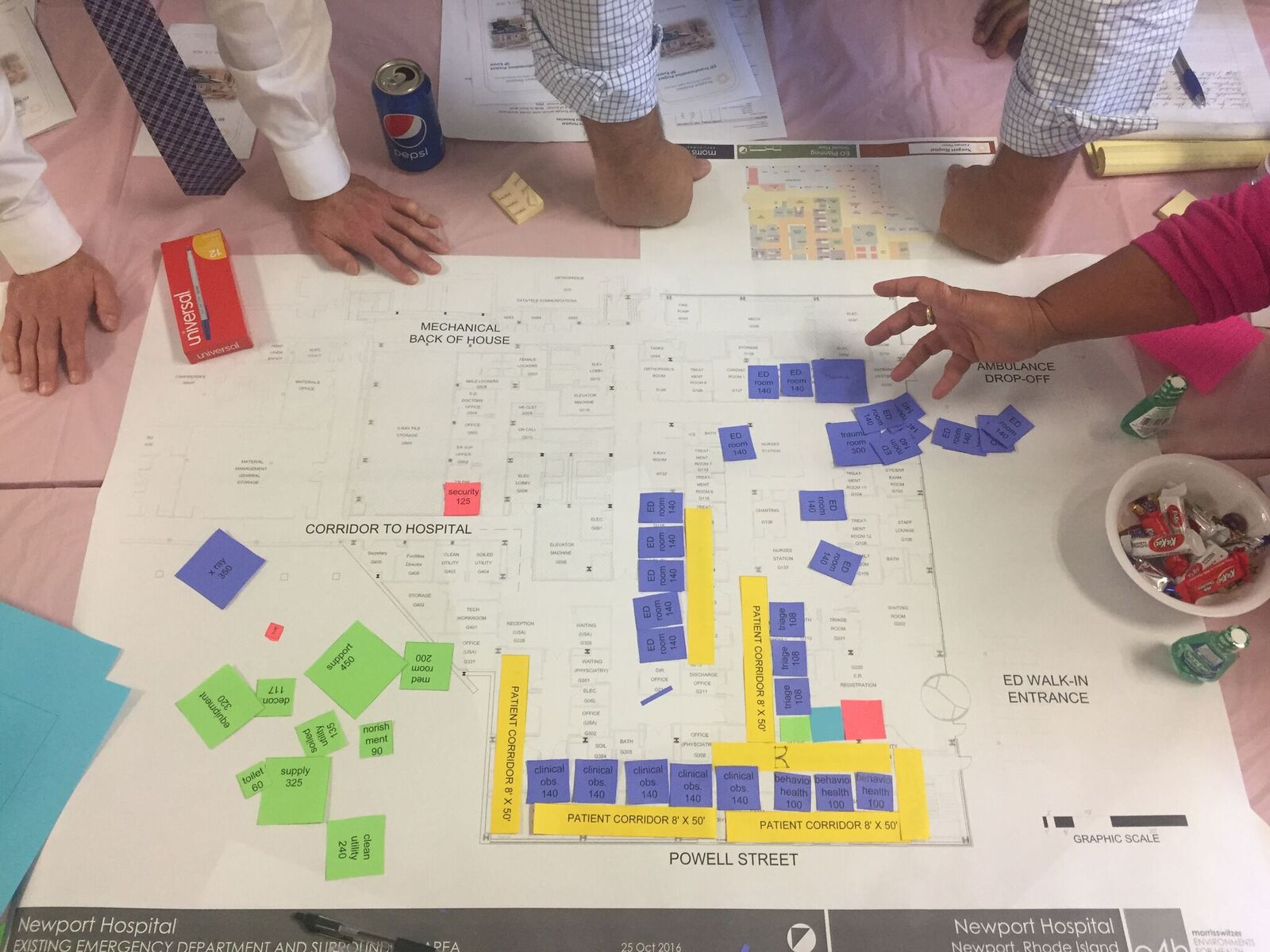
Each 3P team created an adjacency diagram using room blocks from the program. Team members could move rooms around and test out multiple layouts.
With so many stakeholders at the table, there are boundless opportunities to default into group-think. Separating participants into multidisciplinary teams helps ensure each team has enough varied experience to build a comprehensive perspective. It also encourages originality among groups, as even workers within the same department will have different opinions on optimal placement of items and services. Mixing up the teams about halfway through the workshop encourages a new flow of ideas and discourages feelings of ownership of one solution. Having a member of the architecture team serve as a moderator for each group helps keep all participants engaged.
Review the project charter
Every project should have a charter outlining the scope, goals and objectives that have been agreed upon by the architect and hospital administrators. Additionally, most health systems have a set of construction and development standards that workshop participants should take into consideration. It is important to review these guidelines with the entire group early in the process so they understand the final solution’s goal within the broader mission of the facility and health system. In the case of Newport Hospital, design objectives included increasing bed capacity, building a dedicated behavioral health pod and expanding triage services.
Set criteria for success
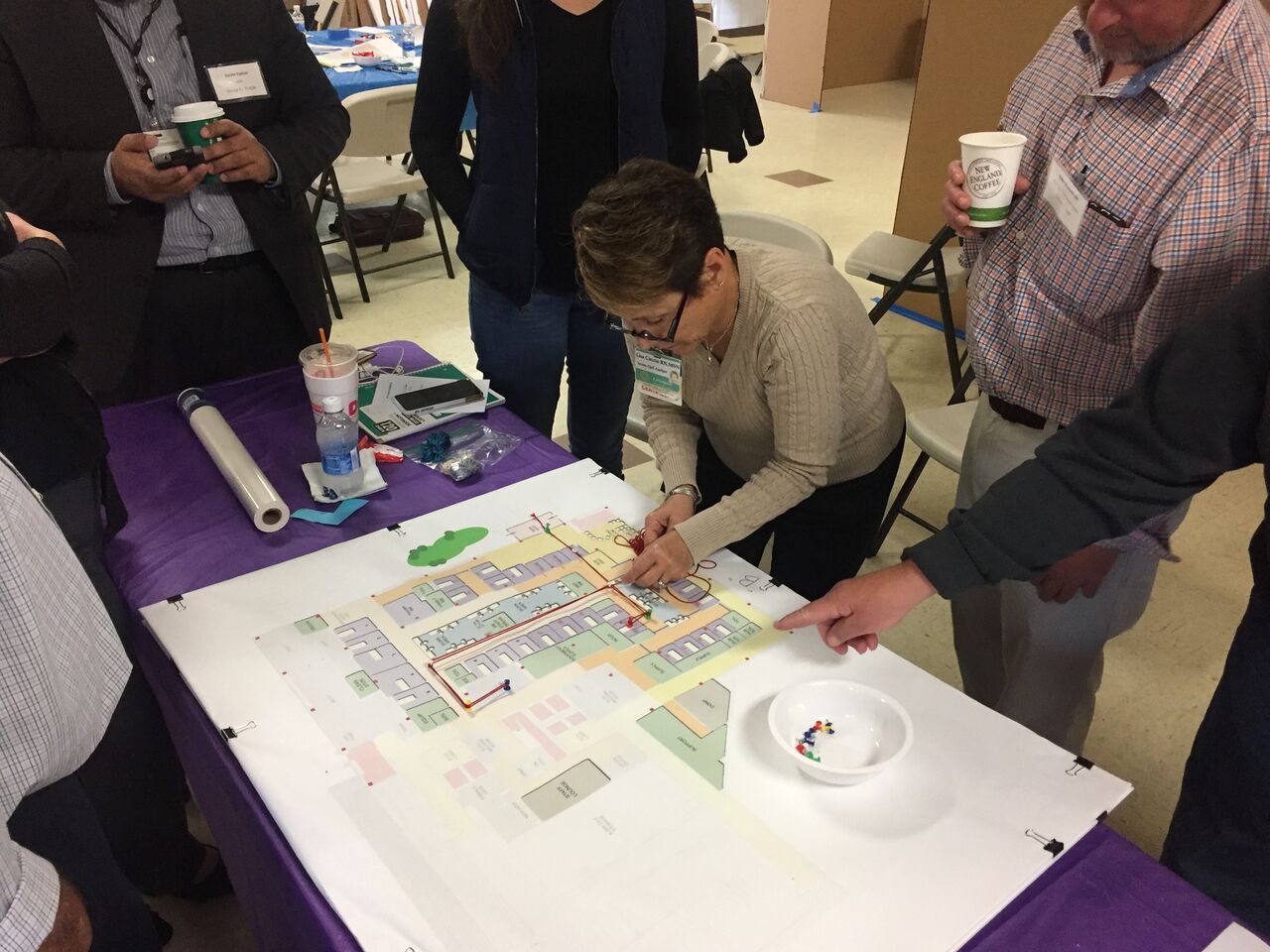
One of the team exercises was mapping out the patient experience. Each team was given a sample patient and traced their movement to each stop on their care path.
To make the most of everyone’s input and set clear expectations for the final design, determine what metrics the team will use to score different iterations and how important each criterion is to the desired outcome. Common criteria include “accommodating increased patient volume,” “allowing increased security presence,” “enhancing patient privacy,” and “supporting clear registration and discharge processes.” These criteria guide the teams as they construct their ideal flow maps and help maintain focus on the priorities of the project. When it’s time for each team to share their proposed design, the larger group can evaluate each option by these defined measures of success.
Keep an organized agenda
Mitigate any fear of the process by letting participants know what to expect. Make sure each day’s schedule is clearly communicated and daily activities are tied to specific goals that support the overall process objective. On the first day at Newport Hospital, we identified challenges and roadblocks in the current workflow and how they might be resolved; day two focused on adjacencies and evaluating where critical spaces would be best positioned; by day three, we were testing schematic design options via 3D representations and finalizing the facility plan. Having incremental goals distributed across all three days also helps participants feel a sense of accomplishment and ensures that the Production Preparation Process moves forward.
Use hands-on tools
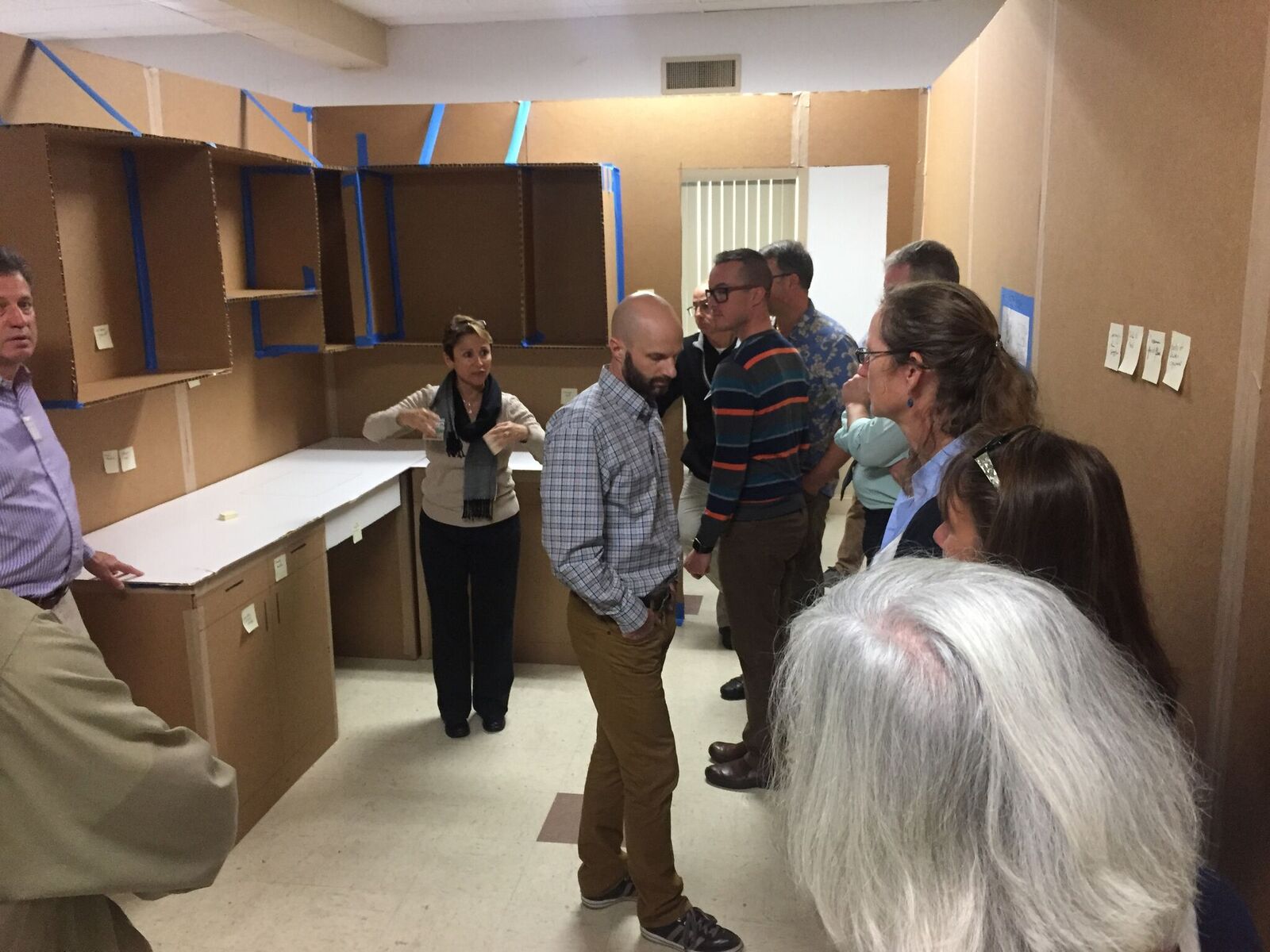
Groups explored physical room mockups and provided feedback to the design team about the best location for casework, equipment and furniture.
A kit of color-coded shapes, scaled to a proposed space program, invites participants to reason through key adjacencies and assemble conceptual space plans. Boards printed with the general space footprint provide the backdrop upon which color-coded cut outs may be arranged and rearranged by multiple team members. For Newport Hospital’s ED transformation, we used bubble diagrams to outline where treatment rooms, nurses’ stations, and other critical spaces would be best positioned, and diagrams with push pins and string to map movement patterns. These simple visuals make it easy to present team diagrams to the larger group for discussion and deliberation. We built life-sized cardboard mock ups to demonstrate the possible design of critical rooms, instigate conversations and foster true understanding. With the latest virtual reality technology, we were able to take this mock-up one step further. Using true-to-scale VR models and headsets with motion tracking, users could move around the virtual ED as though it were built. Participants took turns exploring with the headset while the larger group followed along with the projection, giving feedback and marking up the 3D model in real time.
Build consensus
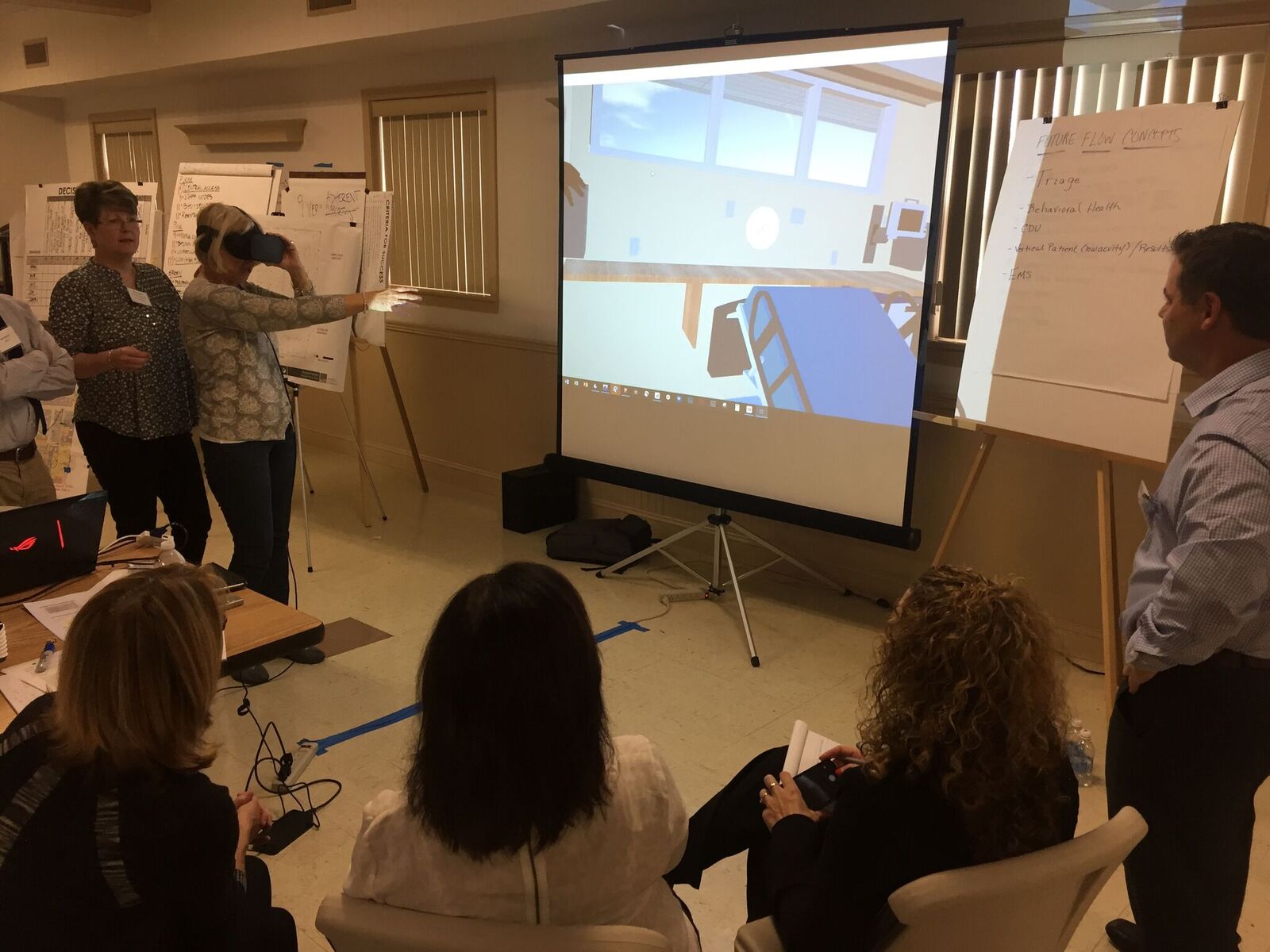
A Virtual Reality mockup. Each team evaluated an Observation Room using VR to explore, comment and make decisions on preferred layout.
After sharing their ideas in this multi-day workshop, it is critical participants feel their input is valued and incorporated. Utilizing the criteria for success matrix established on day one, have teams score each design and only the highest scoring solutions advance to the next activity. This process encourages continued refinement of a “successful” design. Across the three days at Newport Hospital, individual teams vetted all proposed design solutions with the larger group. Ballots were tallied and the highest-scoring options were modeled in the computer. The final design incorporated criteria that were deemed important to the majority of the stakeholders and created greater efficiencies for workers and patients alike.
Design of Lifespan Health System’s Newport Hospital Emergency Department is now complete, expanding the number of treatment bays, triage capacity and waiting room and entrance space per the workshop participants’ direction. By successfully engaging stakeholders in a collaborative design process, Newport Hospital is ensuring that the new ED will be well-positioned to meet the needs not only of its patients but also of its employees, now and going forward.
Regan Henry, PhD, AIA, LEED AP, LSSBB, and Mike Bennett AIA, EDAC, LSSGB, are health care architects at E4H Environments for Health Architecture, an architecture and design firm exclusively focused on healthcare and health innovation.
Images courtesy of E4H Environments for Health Architecture
You must be logged in to post a comment.