Refining a Brooklyn Sugar Factory for Today’s Office Market
The adaptive reuse of this 150-year-old landmark was like “building a ship in a bottle.”
After recently undergoing an extensive adaptive reuse process, The Domino Sugar Factory building in Williamsburg is now part of a bustling zone on Brooklyn’s waterfront. The 150-year-old plant closed down in 2004, but three years later, the New York Landmark Preservation Commission designated three components of the property as a landmark site, a classification that would mark a turning point in its history. In 2012, Two Trees Management acquired the factory for $185 million, and immediately embarked on a complex redevelopment process to harmoniously blend the building’s past with its future.
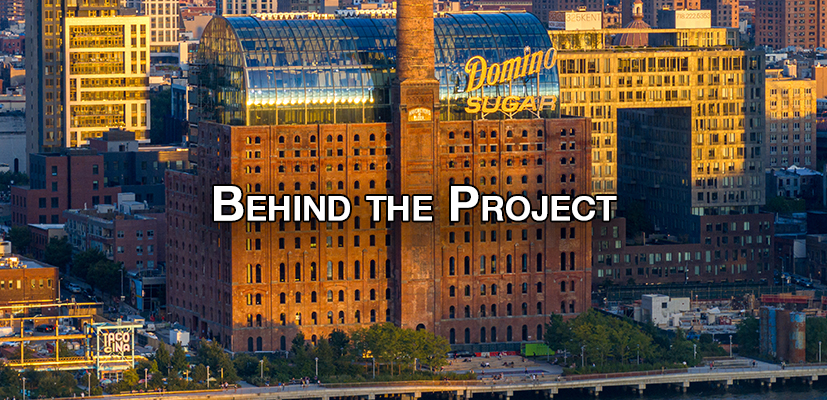
The Refinery at Domino was originally built in a Romanesque Revival architectural style. Image by Max Touhey, courtesy of PAU
The new owner tapped architectural firm Practice for Architecture and Urbanism to reimagine the former factory and transform it into an office complex. The redevelopment resulted in a façade that pays tribute to the old structure, while inside a glass building was added within the walls of the factory, complete with amenities fit for contemporary use. In late September, The Refinery at Domino officially opened as a 15-story office building that offers communal workspaces, a private club, an event space in a 27,000-square-foot glass dome penthouse, conference rooms and an indoor vertical garden.
In an interview with Commercial Property Executive, PAU Managing Principal Ruchika Modi revealed details about the challenges the architectural team faced in the process of transforming the historic building into an iconic 21st century hallmark.
READ ALSO: Enhancing Work Environments Through Creative Offices
How did this project take shape? When did the idea of transforming the factory into an office building first spark?
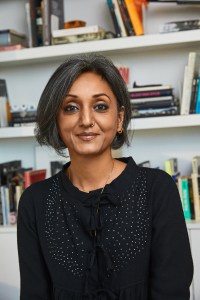
“The construction process was like building a ship in a bottle,” Ruchika Modi confessed. Image courtesy of PAU
Modi: In 2012, PAU’s founder and creative director Vishaan Chakrabarti designed Domino Park’s master plan, which envisioned the Domino Sugar Refinery as the plan’s focal point. When Vishaan started PAU in 2015, inviting me to join, I took on the role of Studio Director, helping shape the firm’s diverse portfolio of projects, and overseeing all aspects of the design process. PAU was founded with the ethos that urban architecture and design should connect communities, offering a sense of place and pluralism to consider solutions to omnipresent issues. This ethos is reflected in the way Domino bridges the past, present, and future, as well as the locals, and commercial communities of the surrounding area.
Through conversations with local community stakeholders and residents, we identified bittersweet feelings many felt toward the Domino Sugar Refinery, which was seen by some as symbolic of labor strife and New York’s inequitable industrial past, and now, urban development. The connection between the site’s history and the Williamsburg community allowed us to better understand our role in preserving the historic site while adapting it to cater to the needs of the current population at large. With the resulting plan, we created 425,000 square feet of state-of-the-art office space, with a ground floor that seamlessly connects the neighborhood to the waterfront park and will eventually include food and beverage retailers as well.
Were there any changes you had to make throughout the years and how are they reflected in the completed project?
Modi: The idea to create a biophilic environment within the 12-to-15-feet gap of space between the original brick façade and the new glass building, filling the gap with luscious greenery, including pin oaks that will reach up to 70 feet, as well as a plethora of hanging plants, vines and succulents, was an aspect of the design that was developed during construction, led by landscape architect Field Operations and a local horticultural society. Another significant improvement to the original design was the removal of all gas-fired equipment to make the building all electric-powered—a critical move that aligns with the city’s ambitious sustainability goals.
What were some of the methods you used to bridge the gap between the building’s original features and the need to create a contemporary space?
Modi: The structure was built to consolidate three functions inside three conjoined buildings—the filtering, panning and finishing of sugar—that required the use of enormous equipment housed in cavernous, multistory spaces purposefully obscured by the repetitive punched arch windows in the masonry. Although these windows were misaligned across the four facades, together they give the entire structure a singular, monumental appearance, crowned by the muscular smokestack on the west elevation built out of radial brick.
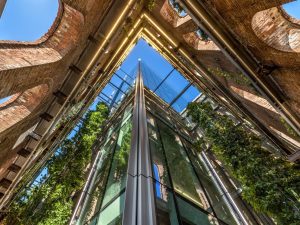
The glass office building took shape inside the original structure. Image by Max Touhey, courtesy of PAU
Rather than navigating the misaligned floors and windowsills across the combined masonry shell, PAU adopted a different approach: nesting a brand-new building into the existing envelope, with a 10- to 12-foot gap between the new and the old. By pulling back from the original walls, ideal and standardized floor heights can be achieved, creating best-in-class office space that is designed to meet the needs of new tenants.
The array of historic windows, uninterrupted by interior partitions, reveal expansive views of Manhattan while allowing the extant structure to be appreciated in an unobstructed form. The light and airy perimeter provides a unique experience and enhances natural light penetration into the core. Rising above and in celebration of the historic structure will be a new glass barrel vault, echoing the American Round Arch Style and singular muscular form in which the original refinery was rendered.
What were some of the challenges you faced during the redesign of this adaptive reuse project and how did you overcome them?
Modi: The biggest challenge in designing the building within a building where the floors do not touch the historic façade was to devise a way to brace the latter in the most unobtrusive and elegant manner while addressing issues of thermal break and weather-tight detailing at the curtain wall. Steel braces tie the ring beams that hold up the masonry façade back to the new building’s superstructure. Along with Silman, our structural engineers, we designed a thermally broken, steel knife-plate thin enough to penetrate it with bent plate connections to the ring beam at the brick wall. This created a tricky curtainwall detail that was resolved through an invention by Focchi, the curtain wall fabricator, of a custom ingenious gasket that would allow the knife-plate to penetrate through the curtainwall, without altering its uniform grid and appearance while at the same time maintaining a watertight seam.
Moreover, the construction process was like building a ship in a bottle but where the bottle needs to be carefully braced during construction or else it will collapse. The temporary bracing of the masonry façade was a construction project in and of itself with its own set of construction documents produced by Silman. We couldn’t demolish the historic structure, which was holding up the façade without first bracing the walls but in a way that wouldn’t interfere with the new permanent structure to follow. Steel towers were erected abutting the exterior of the walls on all four sides, which braced them during the construction of the new building. The historic structure was then dismantled piece by piece.
The new structure was then erected following which the temporary towers were removed. It was a careful choreography where the design and exact location of the existing, the temporary, and the permanent structural elements all had to be coordinated in a way that there were no conflicts and that construction workers would have access to all the parts through the dense network of steel being sequentially installed and dismantled.
What is the one thing that sets the Refinery at Domino apart as an adaptive reuse project in the current context where there is less demand for office space?
Modi: Despite devising this design ahead of the pandemic, The Refinery envisions the future of office work, offering tenants an alternative to pre-pandemic office life with luscious greenery, waterfront views, and, perhaps most importantly, a unique sense of rootedness in history, place and community that many of New York City’s skyscrapers lack.
PAU’s portfolio also includes the ongoing work for Penn Station, a transit hub that is set to be redesigned for the 21st century. Is tackling landmark spaces something that the company has a particular interest in?
Modi: We have built a practice that attempts to address the pressing issues of our era, a practice decidedly focused on social impact through the tangible improvement of cities. PAU designs lasting architecture and innovative urbanism that connects people to pluralism, place, and planet, a big part of which is revitalizing historic buildings and landmarks that have fallen into a state of dysfunction or disrepair.
Penn Station, a civic landmark, has long facilitated the flow of commuters, residents, and visitors in and out of Manhattan. However, with increased ridership, it has not received the same care and attention required to improve and enhance travelers’ experiences. Our proposed design for Penn Station, in collaboration with HOK and ASTM, will provide travelers and New York City residents alike with a greatly enhanced commuter experience in our post-pandemic world. Our proposal returns a sense of civic grandeur to the station by circumscribing Madison Square Garden in a new podium that fills out the street walls of the block. The plan envisions two main train halls—a soaring Eighth Avenue entrance and a light-filled Midblock hall—that together will restore the civic gravitas that has been absent since the 1963 demolition of McKim, Mead & White’s original edifice.
Can you provide a glimpse into some of the PAU’s other upcoming projects and plans?
Modi: In October, we broke ground on the expansion of the Rock and Roll Hall of Fame in Cleveland, originally designed by I.M. Pei. Similar to the Domino Sugar Refinery project, this expansion will connect the museum to the nearby waterfront and expand the Rock Hall’s public spaces. Last spring, the FAA selected PAU’s adaptable, sustainable design for a new generation of air traffic control towers. Though unintentional, to have a hand in reshaping two of I.M. Pei’s iconic U.S. designs preserves the sense of rootedness in history we try to imbue each of our build with.
How do you envision the future of the adaptive reuse trend going forward?
Modi: If the 20th century was about tabula rasa and reinventing places from whole cloth, we believe that the 21st century is about a sense of palimpsest—writing upon layers of history in a way that preserves and builds on the character, culture and communities that have historically defined a place. Add to that, with the health of the planet as a critical imperative, adaptive reuse can and should be our first resort, where possible, to minimize embodied carbon. However, this approach isn’t always the most budget-friendly in terms of first costs. A ‘stick and carrot’ strategy by policy makers would go a long way to ensure that the needs of a few don’t overshadow the priorities of society at large.
You must be logged in to post a comment.