Platinum Quest: Reaching LEED’s Pinnacle
Three project teams share the rewards and challenges of reaching LEED’s ultimate designation.
By Nancy Crotti
When it rains hard in Fremont, Calif., Ruth Chao can hear water trickling down from her office building roof into tanks that store it for irrigation. “It’s lovely,” Chao said.
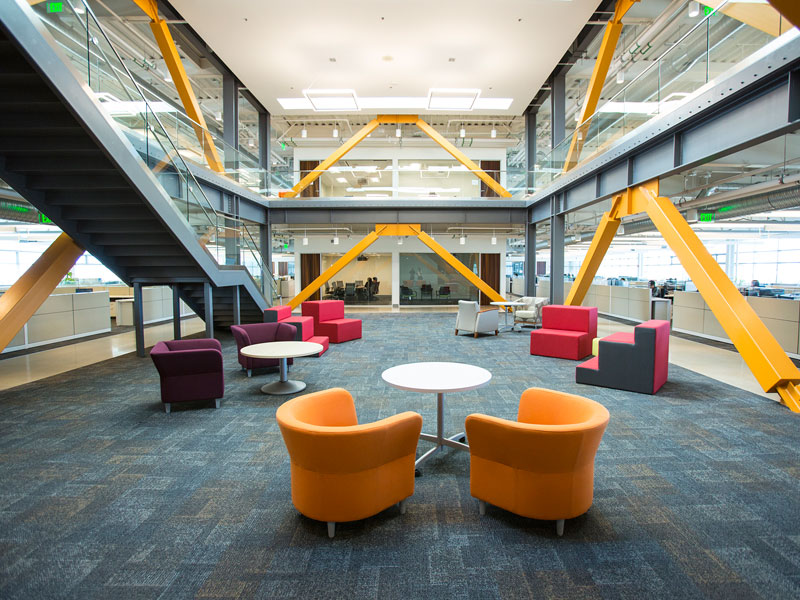
Completed in August 2015, Delta Products’ 178,000-square-foot Fremont, Calif. headquarters is designed for LEED Platinum.
It’s also green, and it could help lead to LEED Platinum certification. As the general affairs manager for Delta Products Corp., Chao works in Delta Americas’ new headquarters. Designed for LEED Platinum certification and completed in August, the 178,000-square-foot building incorporates many of Delta’s technologies. The U.S. arm of Taiwan-based Delta Group manufactures solar energy systems, LED lighting, electric vehicle and hybrid vehicle starter systems, battery packs and wind energy systems.
The building’s geothermal heat and cooling could cut HVAC consumption by 60 percent. A photovoltaic solar system might generate more than 1,000 megawatt-hours per year. Its steel frame allowed for construction with 20 percent reclaimed building materials. Its underground runoff tanks can accommodate up to 140,000 gallons of water; excess will flow to a bioswale. Delta employees can open the windows to let fresh air in and the skylights to let heat escape.
The company nearly abandoned the geothermal component when county water officials balked at a plan for vertical boring, fearing contamination of the nearby San Francisco Bay. Delta switched to directional boring, so pipes would run horizontally to avoid the aquifers beneath its property.
J.J. Pan and Partners Architects & Planners of Taipei and San Francisco-based Korth Sunseri Hagey Architects (KSH) designed the building, which was constructed by Vance Brown Builders of Palo Alto. It is Delta’s 21st green construction or renovation project in the last decade. Incorporating a battery of green features required plenty of coordination. “We had all of our engineers on board early and that made the construction process a lot easier,” said John Walter, KSH project manager.
Windy City winner
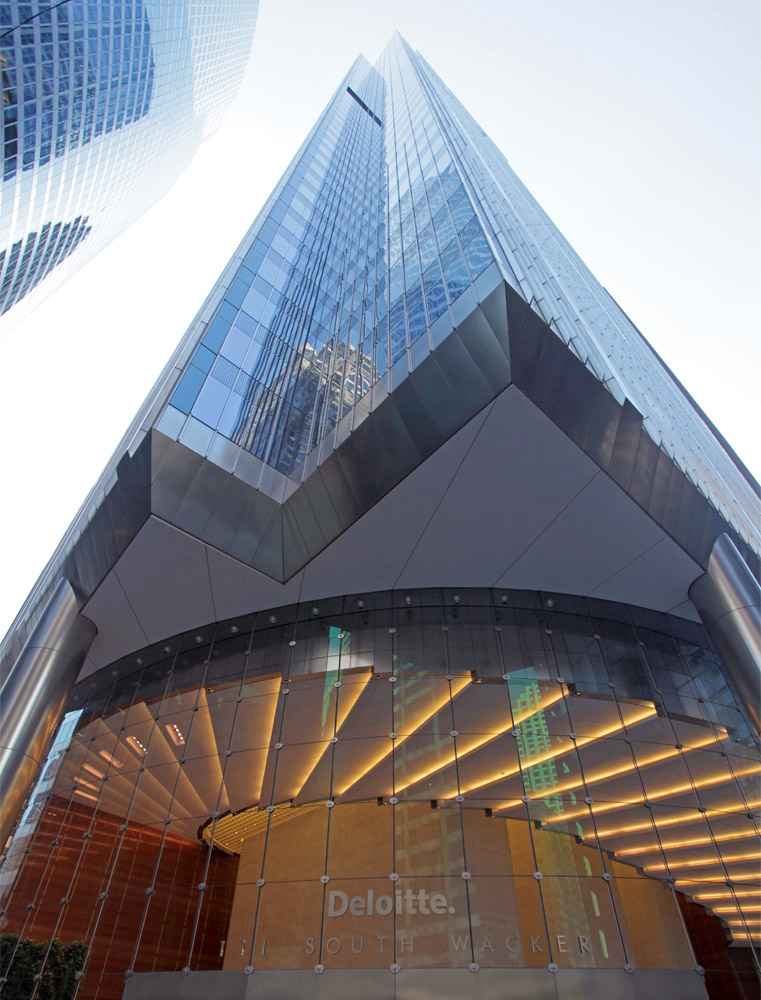
111 S. Wacker Drive, the 1.1 million-square-foot bulding courtesy that achieved LEED Platinum this year.
Taking a building from LEED Gold to Platinum requires upgrades and coordination with tenants. Union Investment, the German fund that owns 111 S. Wacker Drive in Chicago, decided to seek Platinum status in 2011, one year after recertifying it for Gold.
Built by Lendlease Corp., the 1.1 million-square-foot building won LEED Gold status with 66 points when it opened in 2005. Union hired environmental consultant Goby Inc. to recommend upgrades in pursuit of Platinum.
“In Germany, I can tell you that sustainability and energy conservation are much more at the forefront in thinking and in efforts than in this country,” said Thomas Kienzle of Jones Lang LaSalle, the property’s general manager. “They have an inherent desire to protect the planet.”
JLL took over management of the building in 2012 from its developer, John Buck Co. It documented annual water savings of 37 percent or 2.2 million gallons compared with LEED existing-building standards; solid waste recycling at 53 percent, and alternative commuting by tenants at 86 percent. To arrive at that last statistic, Kienzle distributed surveys to each tenant. Distribution turned out to be the easy part.
“Tenants tell you that sustainability and LEED certification are important things, but … you’ve got to bang on doors, you’ve got to pester them until you get what you need,” Kienzle said. “That took most of 2014.”
Kienzle’s team didn’t just pester tenants; it wooed them, hosting monthly meetings for tenants’ green teams with vendors, speakers and raffles of sustainable products.
“It was one of the best, most robust tenant engagement programs that I’ve ever seen,” said Hilary Curtis of Goby, who was 111 S. Wacker’s project manager at the time.
Union invested more than $100,000 in its quest for Platinum. JLL continues to hold green meetings with tenants, which include Deloitte; Locke Lord, an international law firm; and Harris Associates, a private equity firm.
“That’s a testament to the robustness of the engagement program,” said Liz Brady, Goby’s current project manager.
Tysons II’s green trophy
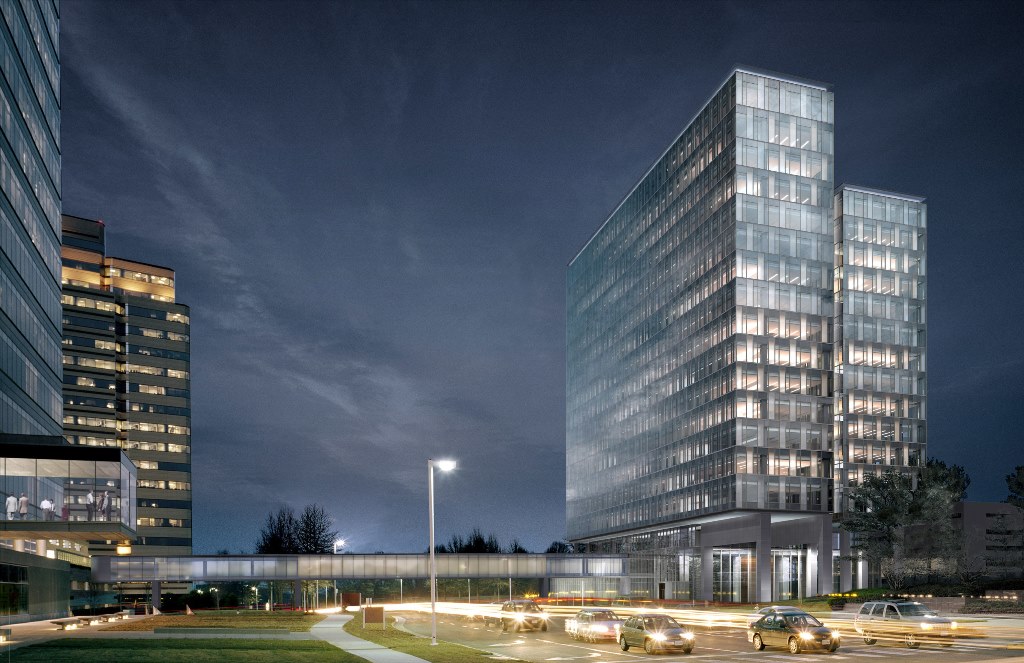
1775 Tysons Blvd. is on track for delivery this spring and would be the first LEED Platinum building in the 117-acre Tysons II master-planned complex.
Lerner Enterprises is betting that LEED Platinum credentials will attract tenants to its new 476,000-square foot trophy tower in Tysons, Va. On track for delivery this spring, 1775 Tysons Blvd. would be the first building in the 117-acre Tysons II master-planned complex to gain Platinum status. It will be the second Platinum winner for Lerner, whose Rockville, Md., headquarters holds the designation.
“As a company, we’re committed to sustainable design,” said James Policaro, Lerner’s vice president of development. “It’s part of our culture. We were very interested in pushing the limit on the sustainable building.”
Kohn Pedersen Fox Associates of New York City designed the office tower, which was constructed by Whiting-Turner Contracting Co. of Chantilly, Va., beginning in 2014. Ernst & Young and Computer Sciences Corp. will occupy 40 percent of the building.
Its sustainable features include high-performance glazing, a chiller system, heat recovery and an efficiency controls system. The centrifugal chillers are arranged in a series with a water-side economizer, an old design that Policaro said has been perfected with modern technology and smart engineering. This, plus a comprehensive metering system, will enable tenants to monitor and measure their energy consumption. Lerner evaluated the system’s performance using a total-cost-of-ownership model over time, as it plans a long-term hold.
Lerner projects an annual energy cost 28 percent lower than that of conventional projects, as well as 40 percent less water use, equivalent to a 1.2 million-gallon savings, Policaro noted. The company expects a five-year payback period for its investment in high-performance energy and water systems.
“Working collaboratively as a team and leveraging the integrated design process enabled the project to source the right materials and build in the right technologies,” Policaro said. “Green features do not necessarily drive cost. Efficiency drives performance, and this project did an excellent job of maximizing the sustainable investments for both the owner and our tenants.”
You must be logged in to post a comment.