Innovation Hits the Airwaves: Inside the 1st Mass Timber Broadcast Facility in the US
Skanska's Jeff Smoker on why Cincinnati Public Radio's new headquarters is one of a kind.
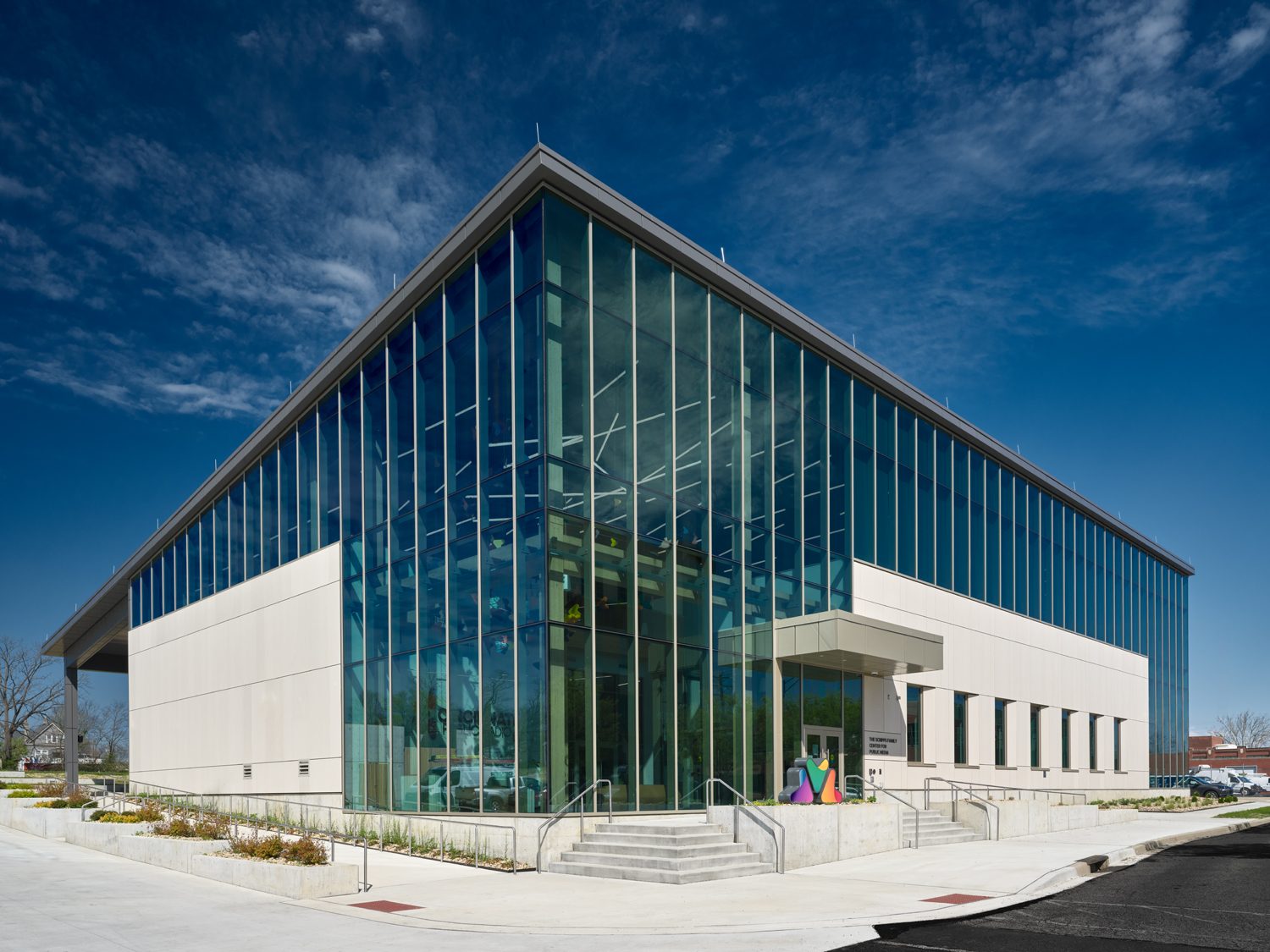
Cincinnati’s Walnut Hills neighborhood is now home to a development unlike any other in the country: a fully mass timber broadcast facility.
Built by Skanska with cross-laminated timber components assembled in just over five weeks, the 35,000-square-foot Cincinnati Public Radio headquarters marks a premier in both design and delivery. The $32 million project is both the first modern mass timber building in the city and the first broadcast center in the U.S. built entirely from cross-laminated timber.
The recently delivered building houses two on-air studios, a podcast suite, a performance space and open offices—all wrapped in a high-performance shell designed to meet tough acoustic and environmental needs.
Skanska brought deep technical expertise to the project and coordinated closely with Emersion DESIGN, WSDG and Nordic Structures to deliver this first-of-its-kind facility. We asked Jeff Smoker, who served as project manager during construction and now works as preconstruction manager with the construction and development company, to take us behind the complex logistics, integrated sustainability and acoustic precision of this milestone project.
Why was mass timber the right fit for this particular project, as opposed to more conventional materials like steel or concrete?
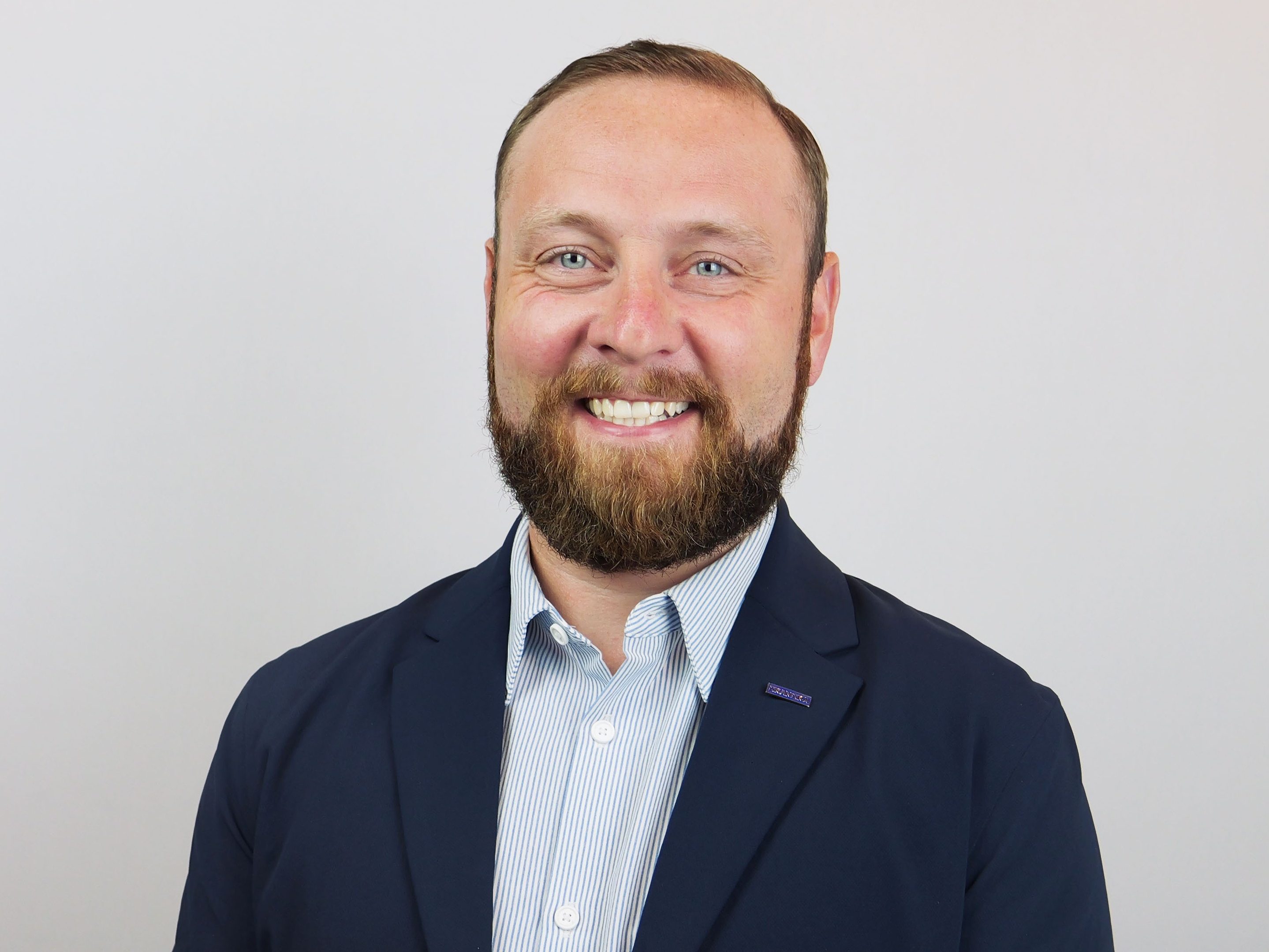
Smoker: When Skanska joined the Cincinnati Public Radio headquarters project, mass timber had already been selected as the primary building material. Our expertise and proven track record with mass timber made Skanska a natural fit for this project. With over 23 mass timber projects completed across eight market sectors and more than 2.3 million square feet of mass timber installed, we were able to bring deep knowledge to ensure a successful project.
Mass timber offers several compelling advantages that make it an ideal choice over conventional materials like steel or concrete. It significantly accelerates construction schedules, as it requires less labor, fewer tools and reduced equipment onsite, allowing for faster assembly and lower overall build time. Mass timber is also a highly sustainable material. As a low-carbon resource, its use reduces the structure’s carbon footprint compared to steel or concrete. The natural wood aesthetic is appealing and can be left intentionally unfinished, which not only adds unique character to the building but also eliminates the need for extra wall finishes, reducing costs.
Were there any site-specific or engineering constraints that made prefabricated timber components more suitable for this project?
Smoker: The project was located on a very tight site with limited access, there was only one way in and one way out. That made things tricky when it came to getting materials delivered and handled. That’s where prefabricated timber really made sense. Because the timber elements were manufactured offsite and delivered ready to install, each delivery could be carefully scheduled as a single truck at a time, minimizing congestion and disruption on the site. This streamlined approach reduced the need for large staging areas or extensive onsite fabrication, which wouldn’t have been feasible given the constrained space.
Any other technical and logistical challenges that you had to overcome to deliver the facility?
Smoker: One of the biggest challenges we tackled was coordinating procurement and delivery of the mass timber across the border from Canada. The timber components were shipped from the manufacturing facility to a holding location where they cleared customs and then they were trucked straight to the job site for immediate offloading and erection. This meant everything had to be perfectly timed, from design approvals and material fabrication to the sequencing of deliveries, so that when a truck arrived, the teams could unload and start erecting right away.
If anything got held up at customs or deliveries fell out of sequence, it would throw off the whole schedule. Trucks would have had to wait until their materials were needed, which would have driven up costs. So, tight coordination and precise sequencing of deliveries were critical to keeping things running smoothly and avoiding delays.
Also, a common challenge when working with mass timber is moisture control. To address this, we prioritized rapid roof installation and invested in a complete reusable weather enclosure system for the building’s exterior to minimize moisture impact on the finished product. After consulting with our Portland team, we chose the RWES system for moisture control as well as to retain the heat necessary for concrete pours and interior fit-out.
Unlike traditional 2x framing with reinforced plastic walls—which are discarded at project completion—the RWES system installs faster, performs better under high winds and rain and can be folded up and reused on subsequent projects. Additionally, it can be customized into assorted sizes to accommodate sloped roofs like Cincinnati Public Radio or to coordinate with the sequencing of exterior skin and curtain wall installation.
How did acoustic and soundproofing requirements impact the development process? Also, how difficult was it to strike a balance between maximizing natural light and creating spaces that have the right light and sound for radio broadcast?
Smoker: One of the key design principles for the building was creating a feeling of openness, something you really see in Cincinnati Public Radio’s open office layout and the architect’s thoughtful use of glass windows both inside and out to bring in plenty of natural light. Wherever there are windows, including the exterior ones, there’s also a layer of 1-inch-thick laminated glass built into the interior walls for extra sound control.
The acoustic consultant, WSDG, applied expert techniques in sound isolation and treatment to create just the right atmosphere throughout the building, from calm and focused workspaces to lively yet controlled shared areas like the gathering space, all the way to production-ready zones for critical listening. Plus, every room features ‘room within a room’ construction to ensure sound doesn’t spill over between spaces.
Tell us more about the lesser-known sustainability features of the Cincinnati Public Radio building.
Smoker: The project used Forest Stewardship Council certified wood, which ensures trees are harvested at a sustainable rate, allowing forests to naturally regenerate and prevent over-harvesting and deforestation. FSC certification also supports biodiversity by protecting ecosystems and wildlife habitats, promotes responsible forest management with strict legal and ethical sourcing standards and helps reduce the environmental impact of construction while supporting long-term forest health.
The building’s main HVAC needs are met through radiant heating and cooling, which provides precise humidity control and allows for a tightly sealed building envelope, key factors for excellent acoustical performance. This system minimizes ductwork, limited only to concealed outdoor air supply and exhaust ducts, boosting energy efficiency and indoor air quality by reducing recirculated air and limiting pathogen spread. CMTA, the mechanical, electrical and plumbing engineer, designed this solution to preserve the clean look of the exposed mass timber, avoiding visual clutter from traditional ductwork.
READ ALSO: The Future of Green Building
The CLT components were built in just over five weeks. Was that your initial projection? What can you tell us about this rapid pace of installation?
Smoker: From a schedule standpoint, the timeline aligned closely with our initial schedule projections. This is based on Skanska’s previous experience working on mass timber projects and understanding how fast it can be erected once material is onsite. Mass timber is a much faster erection process compared to traditional steel or concrete construction.
The installation was quicker thanks largely to the extensive front-end work invested in accurate shop drawing coordination. When all that upfront planning is done correctly, the erection phase becomes much more straightforward, essentially a matter of efficiently picking up the components and putting them into place.
Are you currently engaged in similar mass timber developments in other sectors as well?
Smoker: Yes, currently our Ohio office is working on a project featuring mass timber components. On top of that, we’re in active discussions with two other clients who are eager to explore mass timber for their upcoming projects.
Nationally, we’re seeing a growing trend of mass timber use in medical facilities and we’re also actively working on municipal operations centers. Additionally, several K-12 schools, commercial offices, health-care and higher education projects are currently in the planning stages.
You must be logged in to post a comment.