How to Build Flexibility Into Life Science Projects
Future-proofing is a top priority for tenants of these facilities, observes Anthony Giuliano of Lendlease Americas.
Strong growth in the life science industry continues to drive demand for lab/R&D, manufacturing and warehousing space in the U.S. And while growth in the sector normalized to a more sustainable rate in 2022, limited supply is still fueling a pipeline of life science construction projects—from ground-up developments to renovations to conversions.
Regardless of project type, there’s a common thread: flexibility. By nature, this sector is forward-looking and, as such, facilities must be designed and built in anticipation of technology that, in many cases, doesn’t yet exist. And the ability for life science users to implement that technology without disrupting day-to-day operations is imperative.
While much of this adaptability is incorporated in the design phase, there are a number of construction factors and considerations that are critical elements, too. As an integrated firm with a long track record in this sector, Lendlease regularly helps clients future-proof their facilities through a variety of strategies, some of which are outlined below.
Plan for Robust MEP Systems and Extra Mechanical Space
By nature of the work taking place in them, life science facilities have different physical demands than other property types, most notably in requiring higher power loads, more robust HVAC systems and higher-capacity water and gas lines. At completion, this infrastructure may exceed the immediate needs of the building, but it leaves capacity for new equipment to be added down the road.
Likewise, building in extra mechanical space prepares a life science facility for future equipment switch-outs and upgrades. This can include adding ceiling height during the design stage, programming additional space into equipment rooms, and opting for larger mechanical shafts so that new piping, duct work and wiring is easier to install.
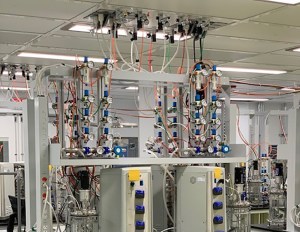
Specialized ceiling utility panels that have plug-in connections for electric, water, gas and any other systems. Photo courtesy of Lendlease
While it’s simpler to plan for upgraded systems and extra mechanical space in new-construction projects, it can also be accomplished in conversions of existing facilities. However, anticipate challenges, such as conflicts in how existing utilities are run from one floor to another and how new piping and ductwork coordinates with the layout of existing building systems. For example, our firm recently worked with Pfizer on a full rebuild of a pharmaceutical manufacturing suite in a building originally constructed for lab/office use, creating what is now one of the world’s largest plasmid DNA production facilities used to support the manufacture of Pfizer’s gene therapy and mRNA vaccine portfolio. The original facility was not designed for the magnitude of MEP services required by the new equipment, so our work entailed significant coordination through computer modeling to demolish, relocate and upgrade MEP systems.
Create Options for Connection Points
Another consideration when it comes to utilities and other building systems—from telecom, to ventilation, to specialized gases—is adding multiple hookup points in lab/R&D spaces so they can be easily reconfigured for a new purpose or project.
One solution we’ve successfully implemented is installing specialized ceiling utility panels that have plug-in connections for electric, water, gas and any other systems—staggered at regular intervals within the ceiling system. If a lab needs to be rearranged for a new purpose or project, it’s simple to unplug each individual lab bench, move it to a new location and plug it back in at the nearest utility panel. And if specialized components need to be added or moved within the lab, it can be done with minimal disruption to operations because there’s no need to add or relocate a connection point, which involves bringing in the appropriate trade and temporarily turning off the service while the new hookup is installed.
Tap the Benefits of Prefabrication
One way to infuse flexibility into a life science project is through the use of prefabricated components, which can be quickly and easily installed as well as disassembled and even reconfigured for different uses. Using preassembled units can be faster and cleaner than traditional on-site fabrication, making this method an especially good match for life science properties that may need to be adapted quickly while maintaining seamless, secure and sanitary operations in adjacent areas of the facility.
Prefabrication has tremendous benefits in the initial build-out, too. For a new manufacturing facility on the multi-building campus of a global pharmaceutical company, we installed 15 prefabricated environmental air system modules containing chillers, air handlers and pumps. The modules were assembled in North Carolina and delivered by flatbed trailers across several states to the project site, where they were lifted into the building by crane and moved into place with an electric forklift. The process took four days, with minimal disruption to the surrounding campus, fewer workers on-site and less coordination needed between multiple trades.
Design with Future Renovation and Access in Mind
For new-construction life science projects, flexibility can be designed in by incorporating elements that make future reconfigurations easier from a constructability standpoint. For example, planning column spacing to maximize span allows more options to rework a floor’s layout down the road. Floor loads can be a hurdle when adding new, heavy components to a space, so designing for extra capacity means not having to add structural reinforcement when switching out equipment. Finally, life science facilities often utilize oversized, unwieldy pieces of machinery, so adding features like demountable partitions and exterior wall panels that can be easily removed and equipment rooms that are near loading docks can make it much easier to move large elements in and out of the building.
The life science space is fast-paced and dynamic, and it’s exciting to work with clients to build facilities that will lead to cutting-edge advancements. One of the most valuable roles a construction manager plays in this process is to anticipate not just what that facility needs in order to function today, but also what will give it the flexibility to continue to perform and support innovation in the future.
Anthony Giuliano is general manager of Life Science Construction, Lendlease Americas.
You must be logged in to post a comment.