Freeze! Read This First Before Developing Cold Storage
Twelve things to know about this unique and fast-growing property type.
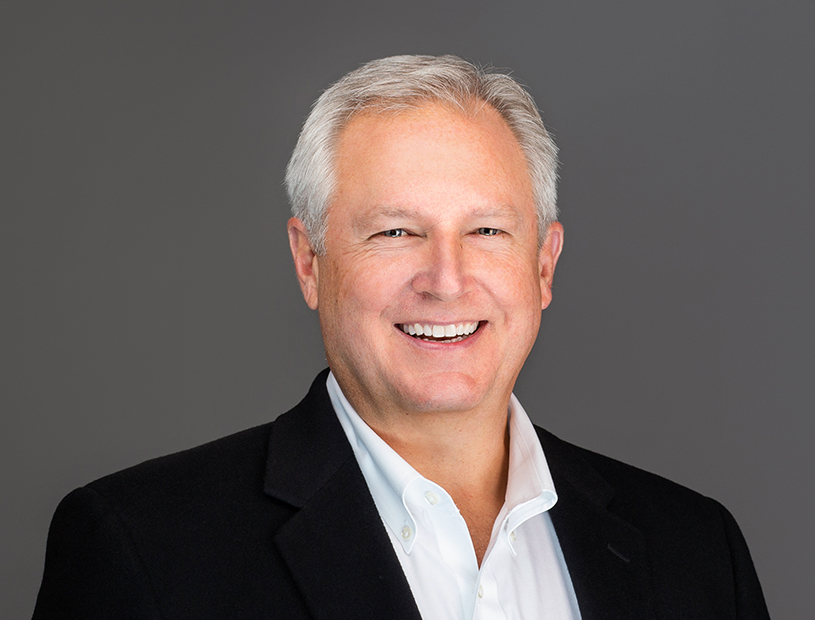
Surging consumer use of online grocery and food delivery services—combined with a need for updated, energy-efficient temperature-controlled facilities—is driving a huge demand for new industrial cold storage facilities across the country.
Online grocery is anticipated to grow 1.7 percent faster than the in-store rate and is projected to be 17 percent of all grocery sales nationally by 2029, according to Food Logistics. Online grocery includes delivery and ship-to-home, which means more temperature-controlled warehouse facilities are needed to support last-mile delivery demand.
LIKE THIS CONTENT? Subscribe to the CPE Capital Markets Newsletter
And much of the existing cold-storage capacity is outdated, with facilities nearly 40 years old and not designed for the technology, safety regulations, processes or pace necessary to operate today.
Since 2020, investment in the cold-storage market has seen steady growth, with $135.1 billion in 2023, $149 billion in 2024, and a projected $341 billion by 2030.
All of which presents ripe opportunities for developers, brokers, investors and general contractors. But site selection, financing and construction of a cold-storage facility all have requirements that differ from standard industrial warehouses.
To be successful in cold-storage facility development, here are 12 important things to consider:
Site selection
When choosing a location for a cold-storage facility, consider key factors like power availability, grid reliability and the physical environment to ensure efficient and uninterrupted operations. For example:
- Power supply: Temperature-controlled facilities require about five times the power of a standard industrial warehouse because electric power runs the refrigeration systems. Look at the proximity of the power lines and how to run power to the site.
- Water flow: You’ll need adequate water pressure to operate the sprinkler systems. Without it, you may need to add a water storage tank.
- Clear height: Today’s cold-storage facilities are taller, with a smaller footprint, particularly in densely populated areas with less available land mass. Confirm what height is allowed. Cubic footage is more critical than the square feet in a cold-storage facility. More pallet positions in the least amount of square footage is key.
- Green space: Make sure to check the local jurisdiction’s specific requirements for green space. Some locations in more populated areas may have enough power and water, but not enough green space.
Construction must-haves
Temperature-controlled facilities have unique structural and material requirements that set them apart from standard warehouses, and these must be carefully factored into development and construction plans. For example:
- Insulation: A cold-storage facility is like a giant insulated box with thermal barriers at the roof, walls and floor. Underfloor heating and insulation are required in all freezer applications.
- Roof design: Because of the thermal barriers, temperature-controlled facilities will require additional roof insulation and structural steel due to the heavy refrigeration equipment that is placed on the roof.
- Dock door sizes: Cold-storage facilities often use continuous vertical levelers for maintenance, sanitation and safety.
- Dry sprinkler system: Freezer and cooler facilities require a dry sprinkler system, while ambient warehouses use a wet sprinkler system.
Financing requirements
Construction of a cold-storage facility is about 2.5 times the cost of a dry warehouse and takes two to three months longer to build. Because of that, there are additional challenges in underwriting these developments. The following strategies can be helpful:
- Add other costs into the lease: The added time and expense in building cold storage make speculative development incredibly risky. While some developers have been successful in building cold storage on spec, we prefer a build-to-suit strategy.
- Underwriting: Cold-storage facilities are expensive, and no two are alike. Due to the high cost per square foot and total project costs, these developments are more difficult to finance. Facilities have different proportions of freezer to refrigerator space. It’s difficult to find comps, making it tough to obtain financing. The deciding factor for us is credit, rent per square foot and location.
- Extended leases: To help underwrite these projects and level out the cost and financing, we have been extending the leases out to 20-25 years for our tenants.
- Add other costs into the lease: In some instances, we will include the cost of the facility’s racking systems into the lease. This gives the end user options on how they want to purchase their racking or material handling equipment.
Looking ahead
The industrial landscape is experiencing a rapid rise in cold-storage demand as consumer habits and new technologies reshape the logistics infrastructure.
Developers are building taller, smarter, more sustainable and more efficient facilities that use advanced automation. Facilities are needed closer to more populated areas to support last-mile delivery demands.
Even with the challenges in financing, we are optimistic about future growth in the cold-storage market.
Don Tuttle, LEED AP BD+C, is director of cold storage for Scannell Properties.
You must be logged in to post a comment.