Resilience Is the Bottom Line in Site Selection
Industrial developers’ key deliverable today is supply-chain efficiency.
Supply chains across a multitude of industries have experienced an unprecedented degree of disruption over the past few years. From food processing to microchip fabrication, warehouses and manufacturing facilities, industrial tenants have all experienced some degree of interruption in their services and delivery times due to a once-in-a-century pandemic, labor shortages, latent economic uncertainty and increasing geopolitical instability.
A September 2022 survey conducted by Deloitte found that more than half of manufacturers nationwide have experienced some or all of the above, coupled with transportation delays, parts shortages and inflated shipping costs.
“We have used the phrase ‘supply chain’ more in the past several years than we have in several decades,” reflected Robert Smietana, CEO of HSA Commercial. “What we thought was normal operating procedure all of a sudden made no sense.”
At a time of elevated consumer demand, omnipresent e-commerce and a rapid reshoring of the nation’s industrial base, the new approach to site selection is one that demands ever-more rigorous considerations of shipping efficiency, utility access and optimal uses of limited land.
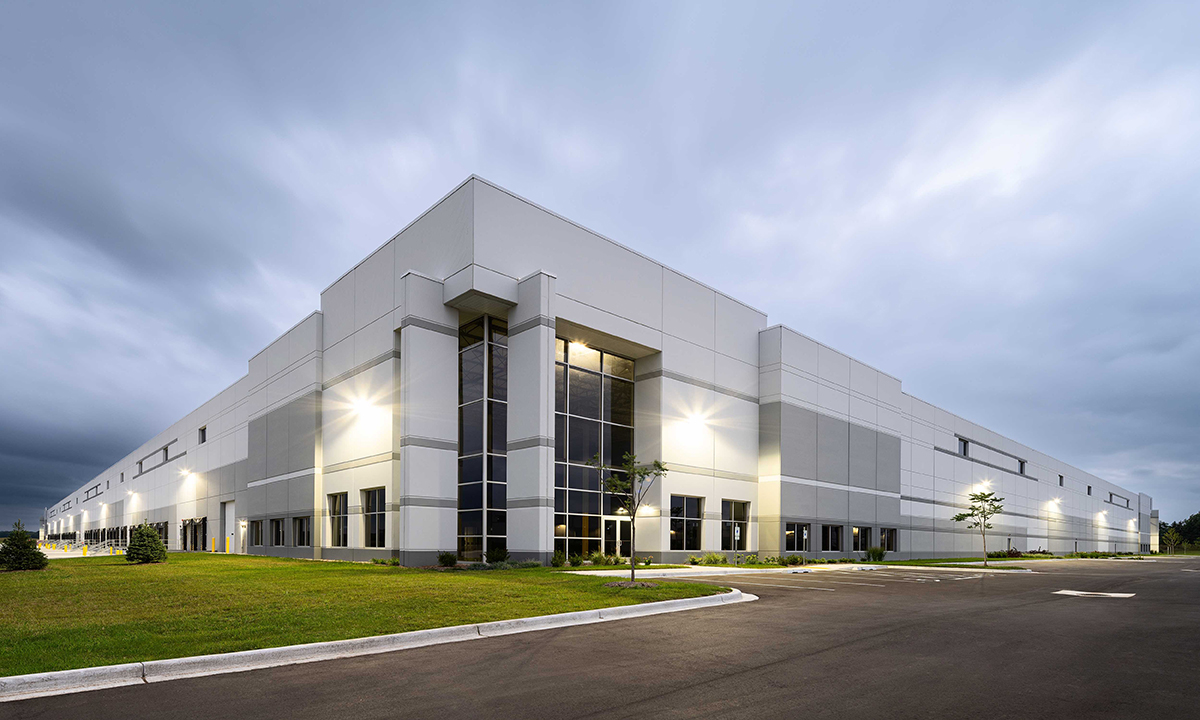
An exterior shot of Bristol Highlands Commerce Center West, one of three buildings in a 1 million-square-foot industrial park located in Bristol, Wis. The facility, a storage warehouse for confectionary company HARIBO, lies less than 2 miles from the manufacturer’s first factory in North America. Image courtesy of Premier Design + Build Group
Avenues of access
In selecting development sites for facilities that can withstand any physical or economic hurdle, a primary consideration is for the ability of goods to move both to and from a facility in a manner that avoids disruption wherever and whenever possible. Through this lens, every aspect of a site’s fitness is scrutinized, from highway and rail access times to power and water delivery capabilities.
“It’s supply-chain real estate,” explained Will Hedges, managing partner of the industrial platform at Triten Real Estate Partners, a Texas-based commercial development and investment firm. “To me, what happens between the demand drivers, the port, the airport and the customer is equally, if not more important, (than) the overall movement of goods.”
For instance, in the Midwest, primarily a hub of distribution facilities and storage for manufactures, a priority is ease of access to as many interstate highways as possible to allow for faster, more reliable shipping.
Another key consideration has been the ability of manufacturers to quickly access stored supplies. “It’s especially important for distribution users who are shipping their product from other centers into smaller locations, or directly from the manufacturers that are supplying those facilities themselves,” explained Mike Yungerman, executive vice president & general manager of Opus Development Co.
With that in mind, HSA helped HARIBO of America, the U.S.-based arm of the German confectioner, lease space 2 miles away from the company’s only North American production plant in Pleasant Prairie, Wis. “(HARIBO) didn’t want to have all their space in one basket, and they like to locate their finished inventory and product for the manufacturing process near them, not on the principal site,” Smietana explained.
Meanwhile, site selection in the West, which combines a large manufacturing base with some of the nation’s busiest seaports, needs to factor in the potential for local labor shutdowns.
“Labor is as critical as it ever has been in the last 25 years of this business,” explained Steve Schnur, COO at CRG, an industrial developer with seven regional offices. “Can people get the labor to service their needs in the warehouse?”
That’s why Schnur’s firm focuses on expected growth and dense population centers. Industrial tenants in the West are also dealing with a reduction of goods coming in from the Pacific. “Someone that brought goods into the country through the ports of Los Angeles and Long Beach may still be looking to do that, but will also bring in goods on the East Coast,” Schnur added.
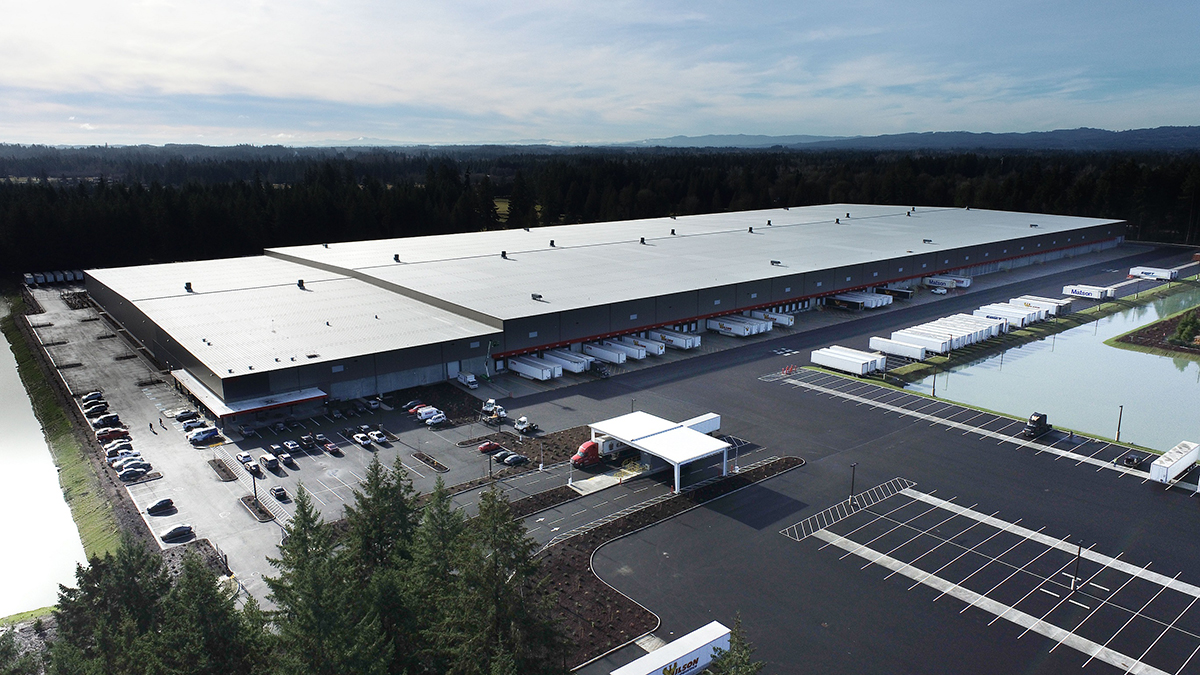
Cubes at Tumwater, a 1.1 million-square-foot distribution center in Tumwater, Wash. CRG developed the facility as a speculative project, eventually designing it to accommodate Costco. The site was chosen in part due to its ability to expand to accommodate more space if needed, as well as its sustainable technological fit-outs. The site incudes a stormwater collection system that prevents flooding, as well as a portion of its parking lot that can be quickly converted to a solar farm. Image courtesy of CRG
Build to suit, built to last
With versatility and reliability in mind, another critical factor in selecting an optimal development site is the technical fit-outs it can accommodate and the resources it offers. A reliable, redundant supply of electricity and water is ever-more important for ensuring reliable operations, particularly as the nation experiences increasingly severe weather.
“These buildings are no longer static racks and a handful of forklifts,” explained Dominic DeRose, managing director at Cresset Partners, which owns and operates facilities in Arizona, South Carolina and Indianapolis, home to much of the nation’s semiconductor and electric vehicle manufacturing. “(These) are advanced, automated systems seeking to minimize the amount of time and effort that it takes to make individual and groups of products,” he added.
Abundant electricity is equally important for storing a variety of products—from perishable food items to sensitive electronics—that require constant temperature controls and bright lights for easy handling and movement to trucks and cargo containers.
“The panels and transformers are double of what a traditional warehouse would use,” Hedges told CPE.
To this end, “an excess” of water is needed for both freeze and fire protection around natural gas lines. “I always like to put my warehouse freeze protection under natural gas because it’s an easy marketing tool that a broker can point to.”
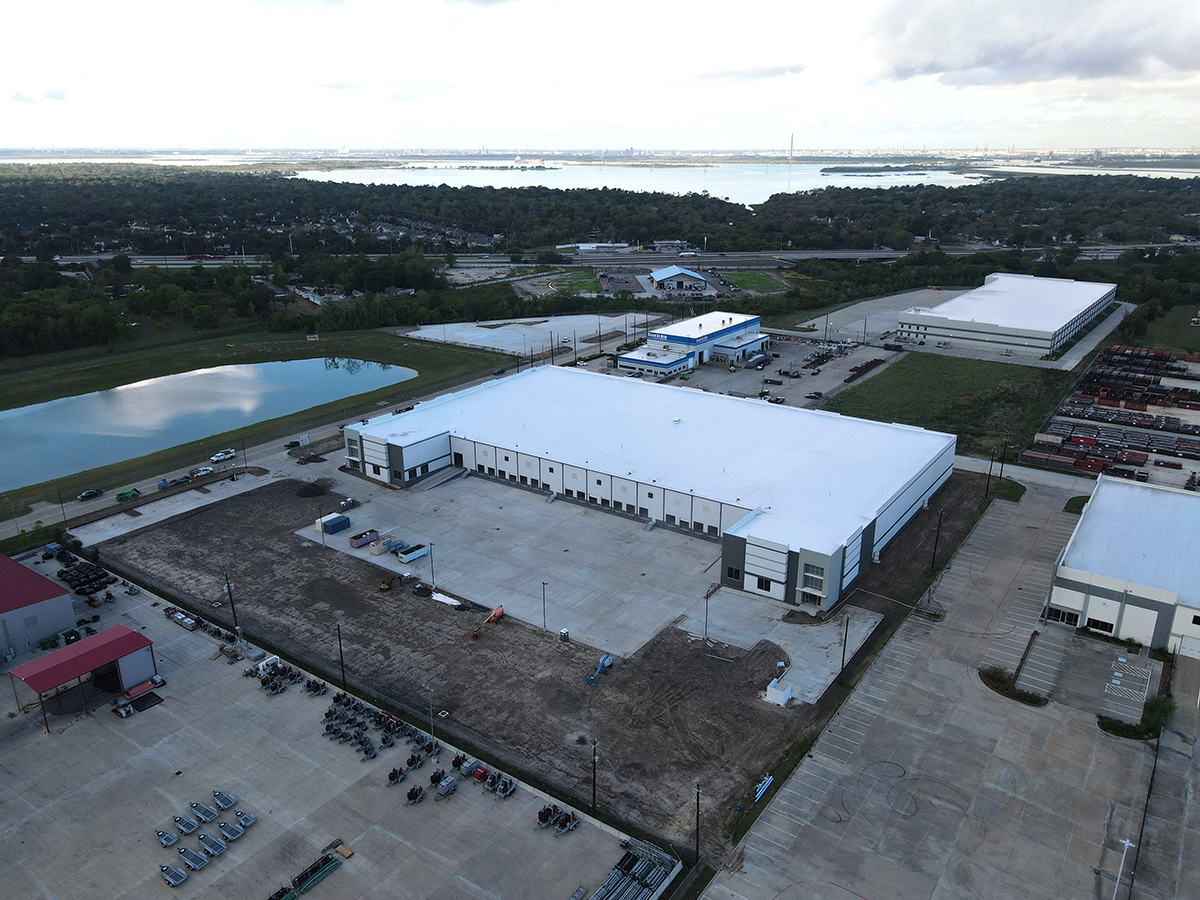
Thompson Distribution Center, a 130,775-square-foot distribution center that is adjacent to the Port of Houston. In developing the facility, Triten Real Estate Partners included several acres of stabilized yard beyond the facility’s truck court, to allow tenants to accommodate more parking in a space-constrained market. Image courtesy of Triten Real Estate Partners
Excesses of essentials
Ample outdoor car, truck and trailer parking are also vital for accommodating a larger workforce and moving goods efficiently. “When you have 100 employees, you need 100 to 200 parking spaces,” DeRose explained.
For resilient distribution, speed in both access to the facilities and in loading goods for transport is the name of the game. “There is a lot of value to a user, from an efficiency perspective, of having either empty trailer stalls ready to get loaded up, or full trailers parked up and ready to be unloaded into the building,” DeRose said.
In some space-starved, highly trafficked industrial districts such as the Port of Houston, developers have had to get creative. At Thompson Distribution Center, a 130,775-square-foot building located adjacent to the port, Triten offers tenants a stabilized yard beyond the property’s truck courts to allow for additional parking.
Maximum clear heights are also a key amenity. Yungerman sees 36- to 40-foot clear heights as the ideal, provided that they comply with local building regulations. “(Users) will have more volume storage in the building and more clearance to accommodate a material handling and racking system,” DeRose noted.
And since tenant needs will change and no two tenants are alike, selecting sites that offer flexibility is also paramount. “We don’t want to back ourselves into a corner by building something that is too specific for any individual user, so that flexibility comes through many different areas in development,” Yungerman concluded.
You must be logged in to post a comment.