Advancing WELLness for Industrial Projects at Greenbuild
The sector is an emerging field for the healthy building movement. Experts offer case studies and strategies.
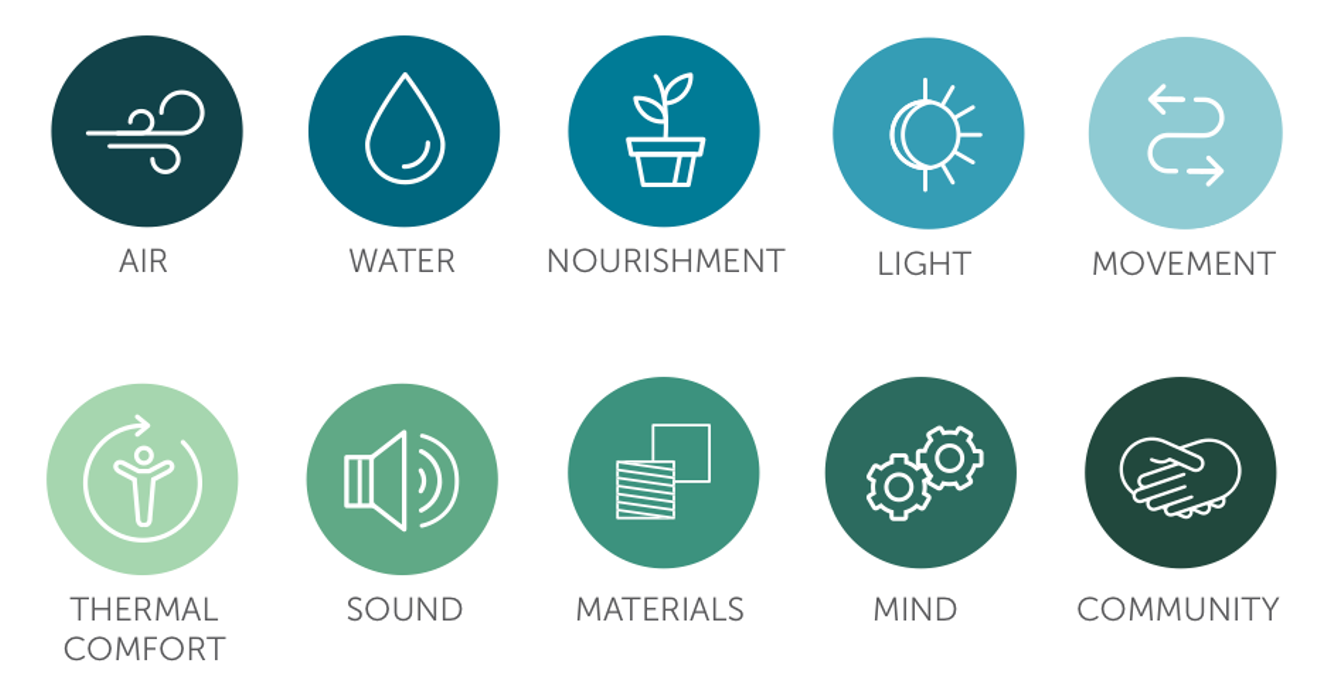
WELL Building Standard concepts. Image via the International WELL Building Institute
The second day of the Greenbuild virtual conference brought together a group of industry executives in a conversation about health in a changing climate, the mission behind the WELL Building Standard and how this rating system can benefit the industrial sector.
READ ALSO: Shaping a Regenerative Future at Greenbuild 2020
The panel on the impact of health and wellness in the industrial sector was moderated by Shalini Ramesh, director of the commercial team at the International WELL Building Institute. Nate Maniktala, principal at BranchPattern, and Chris Fielden, director of group supply chain at innocent drinks, were the speakers.
Building On WELL
Pioneered by Delos and launched in 2014, the WELL Building Standard is a performance-based rating system that has been gaining popularity in the real estate world as it focuses on people’s health and wellness. WELL has been designed to work seamlessly with the LEED rating system. Now on its second version, WELL v2, the standard addresses 10 core concepts:
- air
- water
- nourishment
- light
- movement
- thermal comfort
- sound
- materials
- mind
- community
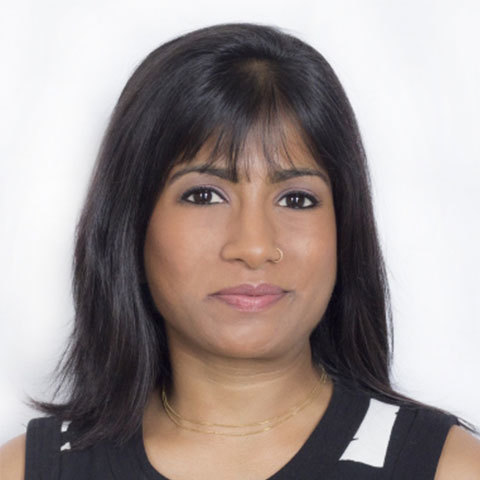
Shalini Ramesh, Director, Commercial Team, International WELL Building Institute. Image courtesy of IWBI
Building on the relationship between human health and planetary health, WELL spans building design and operations, as well as company policies and culture. As people started spending more time indoors—especially since the COVID-19 outbreak—the WELL Building Standard also serves as a framework for responding to the pandemic and preparing for a safer and healthier future.
The certification platform, which is administered by the International WELL Building Institute, currently comprises more than 4,800 WELL-certified, pre-certified and registered projects totaling over 680 million square feet across 64 countries.
Industrial Welcomes Wellness
WELL’s industrial component currently counts nine registered projects and two certified projects: Prologis Park Tacoma, Building D in Tacoma, Wash. (the first industrial facility to be awarded the Silver certification); and the DC5 distribution facility in Prologis Park Tilburg in Tilburg, Netherlands (the first project to achieve Gold certification).
“The industrial sector is still very much so an emerging sector when it comes to WELL, primarily because the requirements are different,” said Maniktala. And that is because, traditionally, the dynamics of the indoor environmental quality of an industrial space have not been as human-centered as it has been for an office building, for example.
Most industrial projects are built on large, decontaminated sites and they are usually situated close to other similar facilities in large industrial parks. These buildings are typically designed for truck traffic and require an optimization of the distribution and logistics aspects, and very little human-centered features are incorporated in this type of project—but wellness opportunities exist, both outside and inside a building.
One of the pilot projects that have seen the implementation of human-centered design is Building 3 of the Rockefeller Logistics Center in Piscataway, N.J. The project, developed by the Rockefeller Group for a global distribution company, totals nearly 200,000 square feet across 18.3 acres.
According to Maniktala, the industrial project was designed to achieve LEED Gold and WELL Silver and, even from the drawing board, it was centered around people. The facility was built on a former chemical site that was decontaminated prior to construction start, as is the case with most industrial developments. By using a modeling tool designed to measure the health and productivity impacts of different design strategies ranging from light to ventilation and acoustics, the project ended up exceeding expectations and qualified for LEED Platinum and WELL Gold.
“We weren’t just going for LEED Platinum for the sake of LEED Platinum,” Maniktala said. “We wanted to make sure the strategies that we were implementing were actually going to create value for the tenant,” he added.
One key component for making value-based decisions on a WELL project is the ability to quantify the impacts. For the Prologis project, energy modeling was used to justify energy efficiency measures and profitability—but always having the wellness aspect in mind, given that a huge part of a company’s costs is directly linked to salaries and benefits for the employees, according to Maniktala.
European Appeal
The WELL Building Standard has also been gaining traction in Europe, where innocent drinks, a growing U.K.-based juice and smoothie company, is building its first-ever manufacturing facility dubbed ‘the blender’. Located within the Rotterdam Food Hub, a business park at the Port of Rotterdam, Netherlands, the project is a $250 million carbon-neutral site designed to serve 17 European countries.
According to Fielden, the project started with five ambitious objectives:
- keep climate change below 1.5 °C (34.7 °F)
- be a sustainable business for the future
- transform the way goods are moved (thanks to its close proximity to where the ships arrive in the port)
- be a great place to work and set an example for industrial design
- inspire wider change by transparent communication and sharing human-centered aspects of the design and building process.
In order to achieve those goals, the blender will feature a canteen with nourishing, affordable food for people who work long shifts and have different dietary requirements, as well as drinking water fountains placed within 100 feet of where everybody is. Additionally, breaks were structured to allow correct rest and recharge for employees in a beautiful environment.
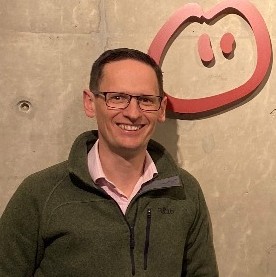
Chris Fielden, Director, Group Supply Chain, innocent drinks. Image courtesy of innocent drinks
Thanks to its position right at the entrance of the Port of Rotterdam, the blender offers stunning views, so the sides of the facility will have ceiling-high windows so that employees can enjoy those views. “That was an expensive choice to do,” Fielden said, “but it was absolutely right: The people working in the factory have the same experience as the people that are working (office jobs) and have this connection with daylight.”
Another human-centered design aspect of the blender was related to bringing color throughout the environment, from offices to the factory’s walls. “Incredibly, that gave a huge challenge to the local planning area, just to be able to put color on the outside of the building,”, Fielden said, pointing toward the fact that most industrial facilities have dull-colored outside walls.
The building also incorporates break out rooms, sound and temperature control through the factory, as well as access to nature both inside and outside the factory—all designed to promote wellness and health among employees.
You must be logged in to post a comment.