Are Office to Life Science Conversions the Answer to Occupancy Woes?
Booming biotech is accelerating this type of conversion. Here's why and how.
Perhaps the biggest question the commercial real estate industry has grappled with since the onset of the pandemic is: What will office properties look like?
Nearly two years after the outbreak of COVID sent office workers home, a clearer view is emerging, and, for many owners, the future involves white coats and Bunsen burners.
Driven by surging demand for biotech space and a rise in office vacancy nationwide, a soaring number of office property owners across the country are considering or are actively in the process of converting their buildings into life science facilities.
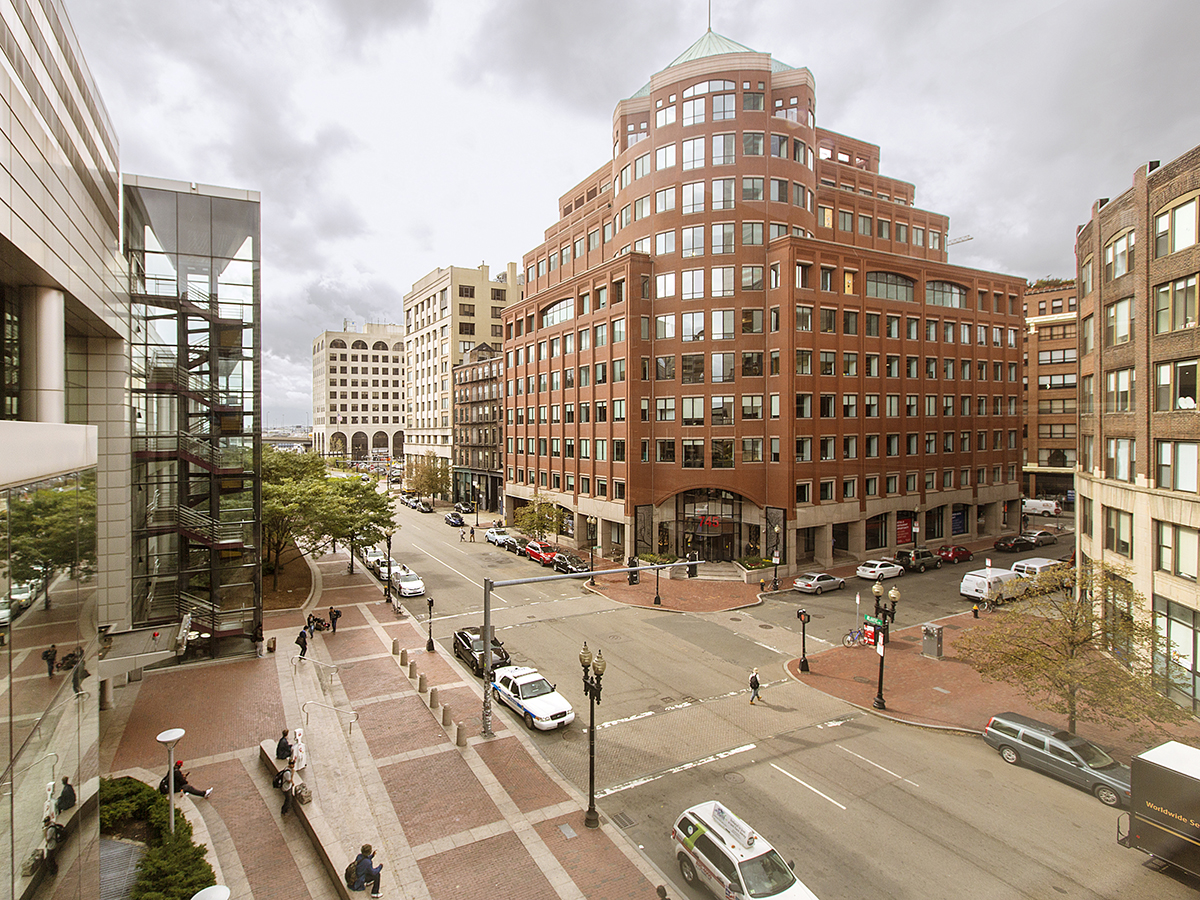
745 Atlantic Avenue is being converted from office to biotech space by Oxford Properties Trust after WeWork announced it would no longer occupy the building.
What’s behind the demand for space? The push to create vaccines for COVID-19 and other diseases, mapping the human genome and other advances in biotech are fueling a decade-long rise in demand for biotech space across the country, according to BOMA. Government funding is also a factor in the rise, as the 2021 National Institutes of Health budget was increased by Congress by 3 percent to $42.9 billion.
And it is not just the government. According to a recent report on the sector from Cushman & Wakefield, a record $70 billion in private and public capital flowed into life sciences companies in North America last year, a staggering 93 percent increase from the previous high of $36 billion in 2018.
Oxford Properties Trust is one of the real estate companies ready to strike on the office to biotech trend. When struggling co-working giant WeWork told the landlord they would break their 131,000-square-foot lease at the firm’s 745 Atlantic office tower in Boston, Oxford decided to transform the building into a life sciences property, adding to the city’s already sizable biotech cluster.
In another example, life science developer Longfellow Real Estate bought a 10-building office park in the Sorrento Mesa area of San Diego with the intent of turning the one- and two-story buildings into lab and research space.
One of the big advantages of converting a building rather than developing a ground-up property is the construction timeline. A new development could easily take three to five years from start to finish, while a conversion typically takes under 2 years, and in some cases less than a year, according to industry professionals.
Despite the sector’s strong fundamentals, the process of converting can be a difficult one. Life sciences spaces require specific and often costly systems and features. Owners looking to convert have a lot to consider, including proximity to other life science real estate, the size and makeup of their existing property, and mechanical, electrical and plumbing (MEP) systems.
Does your building have what it takes?
For those considering converting their office space to biotech space, a smart first step would be a feasibility study.
Devin Bertsch, a senior project manager at Project Management Advisors, has worked in the life sciences real estate niche for nearly 6 years. Bertsch and his colleague, Meris Ota, have seen a big uptick in requests for repositioning over the past two years. The first thing they do is undertake a study to see what it would take to get the conversion done.
“I would say there’s a little bit of a surprise at the level of cost, definitely from a non-life science developer,” said Bertsch. “Dollar per square foot to implement can be a little bit of a sticker shock for those not familiar with the industry.”
Conversions can vary widely depending on the size and needed changes and additions. Cost comparisons can be difficult to make, but at the end of the day, a conversion is typically cheaper than a ground-up development.
“I think it’s fair to say that life sciences is one of the most complex type of buildings,” said Ota.
He suggested owners and investors get a firm handle on their budget, and understand the timing, cost and effort associated with a project of this kind of scope.

A look inside the Aanika Biosciences space at Industry City in Brooklyn. Image courtesy of Industry City
The right team
A successful conversion can’t happen without a team of professionals well-versed in the sector. Building the right team is crucial with projects like this, where so many important factors are in play. A qualified team can help expedite the process in terms of designing, permitting and construction delivery.
“The more diligence up front, the less headaches and disappointments down the road,” said Ofer Ohad, managing partner at DBI Projects, a New York City-based building consulting firm that has worked on life science conversions.
Toronto-based Oxford has invested more than $1 billion in the sector in 2021 alone. In addition to the 745 Atlantic conversion, the company is also completing conversions in Seattle and the Bay Area. Tycho Suter, vice president of investments at the firm, said his best advice for those looking to convert is to find professionals who can think outside the box.
“I would make sure that you have great consultants working alongside you,” said Suter, especially for buildings that may not be ‘perfect’ for conversion. “There are ways to be creative—not all specifications need to check every single box. As long as you can get creative.”
Property size and type
One of the most important factors in an office to life science conversion is looking at the existing structure’s bones. Properties that are lower-rise and have smaller floorplates and higher ceiling heights are typically the ripest for conversion, and easier to work with when installing MEP systems.
“I might be a little old school,” said Tim Martin, a senior vice president at JLL who works in property management. “To me, the infrastructure and ability to perform trumps all.”
Martin, who runs a large portfolio for an owner in Boston’s Kendall Square, said that oftentimes in a conversion, an owner will need to squeeze 2 to 5 times more mechanical equipment in a building than it was designed to hold.
An operator will need to consider the tenants that will eventually be working in the space. Life science tenants can range from R&D companies to prototyping and manufacturing firms. Their work needs require high ceilings, the ability to have heavier loads on each floor, strong loading dock access, and the ability for back-of-house operations and mechanical space.
The team will need to be able to plan how and where building systems will be installed, make sure the new space will be code compliant, and that there is adequate space to store the chemicals and materials that will be used by the future tenants.
Building systems
Highly specified building systems go hand-in-hand with life science and biotech tenants. MEP systems are a heavy component in these kinds of properties, whether they are conversions or new developments. Having a detailed plan of where they will go and how they will fit into an existing building is a key factor in any life science conversion.
“You’re literally trying to fit 50 pounds of demand into a 10-pound bag,” said Martin. “What tradeoffs do you make for that to happen?”
In one particularly complicated project, Bertsch recalled how the floorplate in a building was so small, his team had to remove one of the elevators in order to create shaft space for exhaust ductwork. Adding to the complication, the building was partially leased at the time and there was no other ideal place to put another new shaft.
“We’ve got the puzzle inside the building, and we’ve also got space considerations to solve for outside of the building,” said Ota.
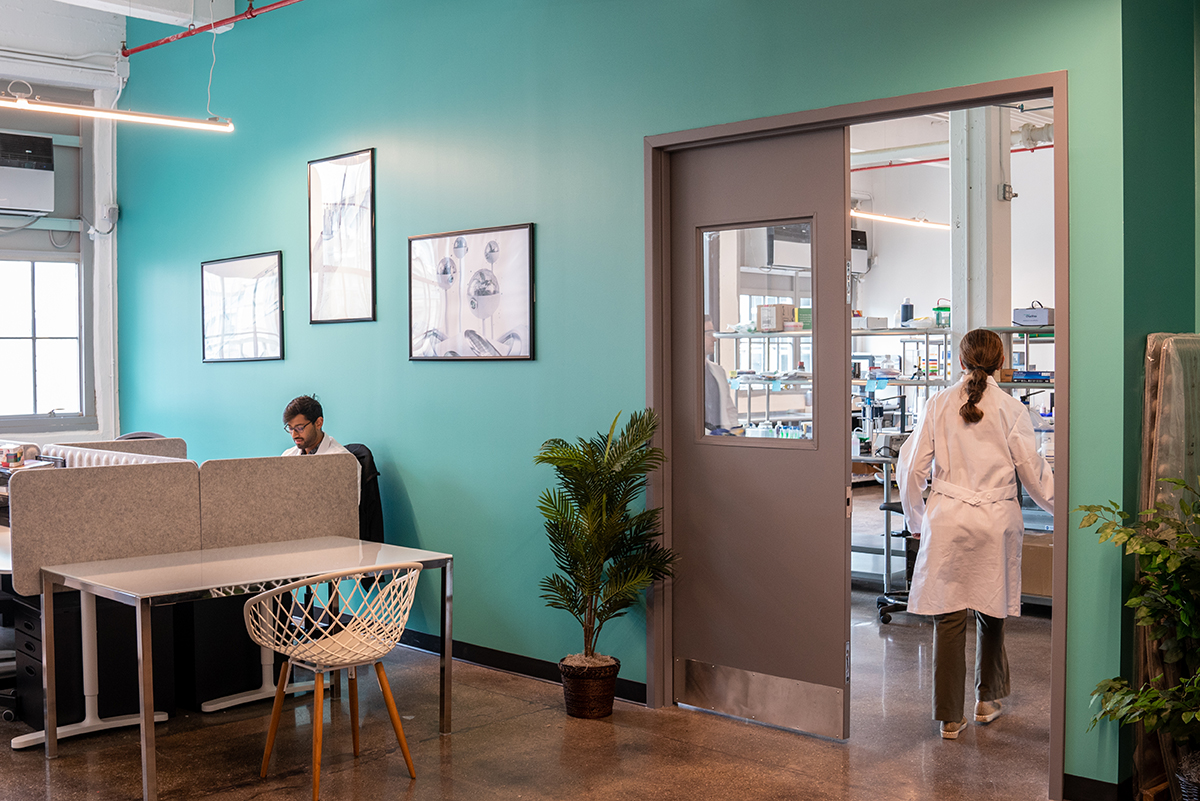
A look inside the Aanika Biosciences space at Industry City in Brooklyn. Image courtesy of Industry City
Location, location, location
Before thinking about anything else, consider the location of the property. Life sciences facilities tend to grow and develop within clusters, the largest of which are in Boston, San Diego and San Francisco. Those clusters do well, in part, because of external factors around them—academic institutions, qualified employees, and the all-important buy-in of the local government. Without these, the demand for space may not be strong.
“There’s definitely a compelling case for being around an ecosystem,” said Martin. “A lot of this work you can’t do from home or remotely, it needs to be done in a controlled, safe environment.”
Life science clusters often grow what some in the industry call a “tentacle” nature, with hubs growing outward into nearby areas. “There’s a saying that capital goes where it’s welcome,” said Ota of the expansion pattern. “Life sciences has a technical layer of complexity that demands a knowledgeable municipal structure to welcome and accommodate that. Nobody wants to be the first developer to a city to educate them. That’s part of the tentacle nature—there tends to be growth where existing growth has established itself.”
Office buildings in a mostly residential neighborhood that may not qualify for the right zoning or are met with resistance from the neighborhood may not be the best situation for a conversion, said Ohad. “It has a lot to do with the building context and surroundings.”
Jeff Fein, senior vice president of leasing at Industry City, has a wealth of experience leasing space to biotech and life science tenants at the 16-building complex in Brooklyn’s Sunset Park. The former industrial site has a wide range of tenants, including biotech companies. “Sometimes the hardest part is getting signoff from the city, not physical delivery,” he said.
You must be logged in to post a comment.