E-Commerce Continues to Steer Logistics Demand
As much as 75 million square feet of new U.S. industrial space will be needed each year through 2030, Prologis estimates.
E-commerce remains a driver of demand in the industrial sector, and its growth will necessitate between 50 million and 75 million square feet of new space each year in the U.S. until 2030 at least, according to Prologis.
The pandemic drove the demand for industrial warehouse space in the early 2020s to new heights. More recently though, demand has cooled—but not completely.
A number of tailwinds are at work fueling e-commerce growth, and thus logistics demand, according to the REIT. These tailwinds include increasing online shopping for groceries and other nondiscretionary goods, but also demographic shifts, such as Millennials reaching peak spending years, and the fact that online shopping tech is more sophisticated than ever, which is facilitating an increase in orders.
Prologis data shows that even as freight volumes gyrate—especially ocean freight, which expanded quickly in the early part of the pandemic and then slowed down—occupied logistics stock has seen a steady uptick.
READ ALSO: Industrial Wellness: Is It Here to Stay?
There is an international component to demand as well, the company noted. Demand growth has accelerated in 2025 as companies shift cross-border fulfillment onshore.
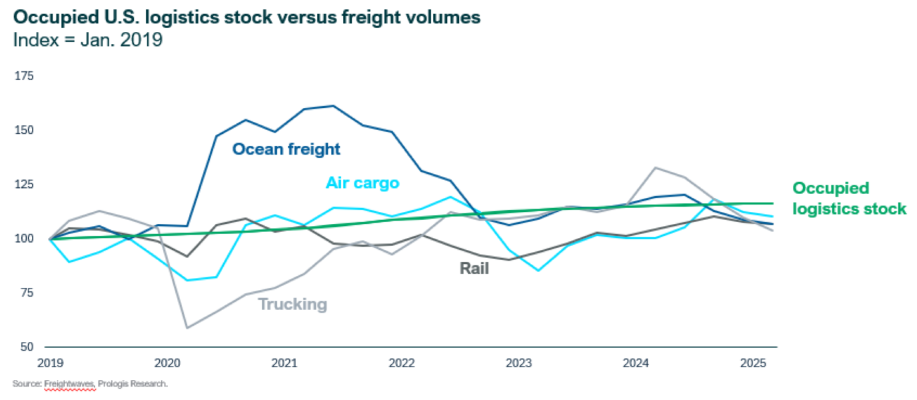
Prologis came to these conclusions by developing a framework it calls Leasing Driver Dimensions, based on its research, discussions with customers and engagement with supply chain experts. The framework offers insight into why industrial space occupiers act the way they do, spurred by different trends.
Near-term demand is a balance between supply chain-related needs and high levels of uncertainty, Prologis posits. Shifting trade policies and economic concerns will impact demand, but even so, companies will continue to invest. They will be driven by demographic expansion, implementation of previously deferred plans from 2023 and 2024, and heightened inventory needs in a time of trade disruptions.
Flexibility and inventory management are critical, Prologis found. Volatile trade conditions are prompting increased utilization of third-party logistics and existing warehousing, the better to ensure supply-chain resilience. Shifting manufacturing locations are reshaping location selection for logistics as well.
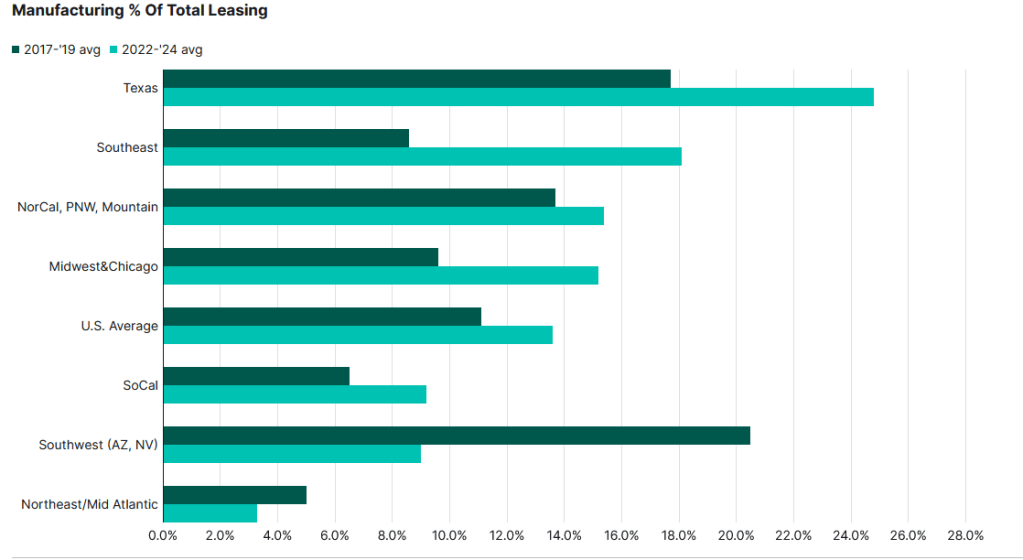
Such sectors as semiconductors, pharmaceuticals and automotive—which are high-value enterprises—are accelerating near-shoring and U.S. production to mitigate geopolitical risks.
Manufacturing’s share of new U.S. logistics real estate leasing has climbed to 14 percent over the past three years, up from less than 10 percent before the pandemic. The shift is most notable in Texas, Chicago and the Southeast—where manufacturing now represents roughly 20 percent of new leasing, up from 13 percent—but is also evident in parts of the Bay Area and Southwest. A key driver: the surge in data center development, which fuels demand for the production and logistics of servers, power systems and specialized cooling equipment.
Lower-value segments, such as plastic goods, apparel, furniture and electronics, are incrementally diversifying production across East and Southeast Asia.
Long-term growth prospects remain strong, Prologis predicts. E-commerce penetration, demographic-driven consumption and urban logistics needs will sustain robust logistics real estate demand, despite the uncertainty of future economic cycles.
Different kinds of leasing strategies emerge
Not all leasing patterns are the same. Nondiscretionary sectors (food, beverage and medical) typically display steadier demand, while discretionary sectors (housing-related products and automotive) tend to be more cyclical, Prologis reported.
Larger, diversified firms maintain more consistent leasing strategies based on their internal business needs, rather than as a reaction to macroeconomic fluctuations.
READ ALSO: Top Southeastern Markets for Industrial Transactions
By contrast, smaller companies with narrower product offerings tend to adjust logistics requirements in real time as economic conditions change. They expand their real estate needs late in cycles and recover more slowly than the big outfits.
Short-term economic uncertainty leads companies to be cautious, both in their growth outlook and in their long-term investing, the industrial specialist found. As a result, companies wait as long as possible before signing a new lease, with space needed urgently after execution.
During periods of less uncertainty—and as more positive economic growth is apparent—leasing sentiment improves and growth occurs at a more regular cadence.
You must be logged in to post a comment.